Reasons for insufficient adhesion of water-based ink in screen printing
Date: Oct 09 2024 From: Star Color Views:
In recent years, many screen printing inks have changed from oil-based inks to
water-based inks, resulting in many quality issues during the printing process, as there are significant differences between water-based and oil-based inks.
Next, we will analyze the reasons and solutions for the insufficient adhesion of water-based screen printing ink.
1. Cause analysis
1. Improper matching of ink and substrate:
The improper selection of ink and substrate results in the inability of ink to effectively adhere to the substrate. For example, the compatibility between the ink formula, connecting material, and printing material is poor, or the ink has expired and become ineffective.
2. Surface issues with the substrate:
The surface of the substrate is not clean, with oil stains, dust, or other attachments, which can affect the adhesion effect of the ink. The tension on the surface of the substrate is lower than that of the ink, which can also reduce the adhesion of the ink.
3. Insufficient ink drying:
Insufficient drying time of ink and incomplete curing of ink can lead to poor adhesion. For example, if the heating is not sufficient, the printing drying speed is slow, or the lower ink layer is not completely dried and covered by the new ink layer during overprinting, false drying may occur.
4. Improper printing process parameters:
Printing speed too fast, insufficient printing pressure, thick or thin ink layer, and inappropriate screen tension may all affect the adhesion of ink.
2 Solution
1. Choose the appropriate ink:
Select ink that matches the material and characteristics of the substrate. For example, when printing metal substrates, epoxy resin should be used as the connecting material resin in the ink; When printing polyethylene plastic, polyethylene should be used as the connecting material; When printing polypropylene, polypropylene should be used as the connecting material.
2. Pre treated substrate:
Pre treat the substrate, such as polishing, cleaning, etc., to improve its surface energy and enhance the adhesion effect of ink. Thoroughly clean the surface of the substrate with a cleaning agent to remove any oil stains, dust, and other attachments on the surface.
3. Adjust the ink drying time:
Adjust the drying time of the ink based on its characteristics and the material of the substrate to ensure complete curing of the ink. For ink with too fast drying speed, appropriate slow drying agents can be added; For inks with slow drying speed, quick drying agents can be added.
4. Optimize printing process parameters:
Adjust the printing speed to avoid uneven ink dispersion or poor printing results caused by being too fast or too slow. Adjust the printing pressure to ensure that the ink can be fully transferred to the substrate, while avoiding damage to the substrate caused by excessive pressure.
5. Add additives:
According to the needs, appropriate additives such as leveling agents, adhesion promoters, etc. can be added to improve the adhesion and printing effect of the ink. Pay attention to the amount and usage of additives to avoid negative effects caused by excessive or improper use.
6. Surface modification of printing materials:
For printing materials such as plastic films, the content of polar groups on the surface can be increased through methods such as corona treatment and plasma treatment, thereby improving the adhesion of ink. For metal surfaces, oxidation layer removal treatment can be performed to enhance the ink's wetting ability.
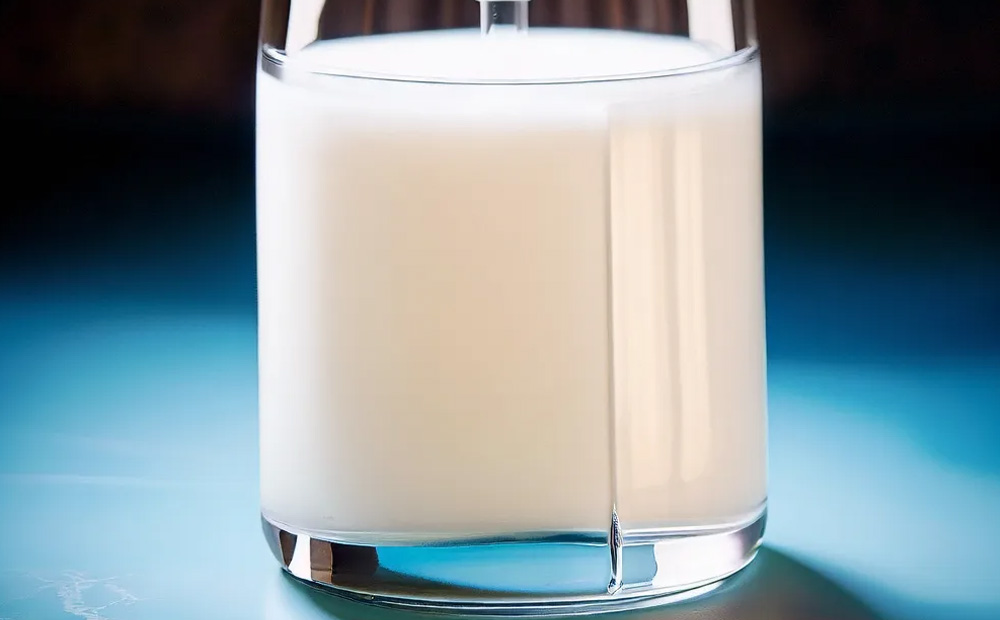
The above are the reasons and solutions for insufficient adhesion of water-based ink for silk screen printing. The problem of insufficient adhesion of water-based ink for silk screen printing can be solved by selecting suitable ink, pre-treatment substrate, adjusting ink drying time, optimizing printing process parameters, adding additives, modifying the surface of the printing material, strengthening equipment maintenance and operation skills training, and conducting adhesion testing.