What is the viscosity of UV flexographic ink
Date: Jul 01 2024 From: Star Color Views:
In the
UV flexo printing process, the viscosity of the ink is one of the critical factors affecting print quality and effectiveness. Selecting the appropriate viscosity of UV flexographic ink is crucial for ensuring print quality and efficiency. When adjusting viscosity, various factors such as printing equipment, printing materials, image details, and expected printing results need to be considered.
The viscosity of UV flexographic ink typically ranges from 200 to 600 centipoise (cps). This range facilitates good fluidity and transfer performance during the flexographic printing process. Specific viscosity values may vary depending on the brand and application requirements, so referring to the technical data sheet provided by the ink manufacturer is an effective way to obtain accurate viscosity values.
When data from the ink manufacturer is not available, technical means need to be used to test the viscosity of the ink. So, how does ink viscosity affect printing? Let's compare high and low viscosity inks from various aspects:
Print QualityThe viscosity of the ink directly affects print quality:
High viscosity: May lead to poor ink transfer between the plate and substrate, resulting in blurred images or ink accumulation defects.
Low viscosity: May cause excessive ink flow, resulting in uneven printing, inconsistent colors, or missed prints.
Dot ReproductionViscosity affects dot reproduction capabilities:
High viscosity: May lead to reduced reproduction of fine dots, causing dot enlargement or deformation, affecting image fineness.
Low viscosity: Easier to reproduce fine dots, but excessively low viscosity may result in unclear printed images.
Color Saturation and BrightnessViscosity has a significant impact on color performance:
High viscosity: Typically provides higher color saturation and brightness as it ensures sufficient ink transfer to the substrate.
Low viscosity: May result in insufficient color saturation and brightness, making the print appear dull.
Drying SpeedViscosity affects the drying speed of the ink:
High viscosity: May require longer UV curing time as inks with high viscosity tend to have higher concentrations of photoinitiators and resins, resulting in a slower curing process.
Low viscosity: Typically dries faster, but excessively low viscosity may lead to thin ink layers, affecting curing results.
Adaptability to Printing EquipmentViscosity affects the adaptability of the ink to printing equipment:
High viscosity: May require adjustments to printing equipment settings, such as increased pressure or speed, to ensure uniform ink transfer.
Low viscosity: Generally easier to adapt to various printing equipment, but still requires appropriate adjustments based on specific conditions.
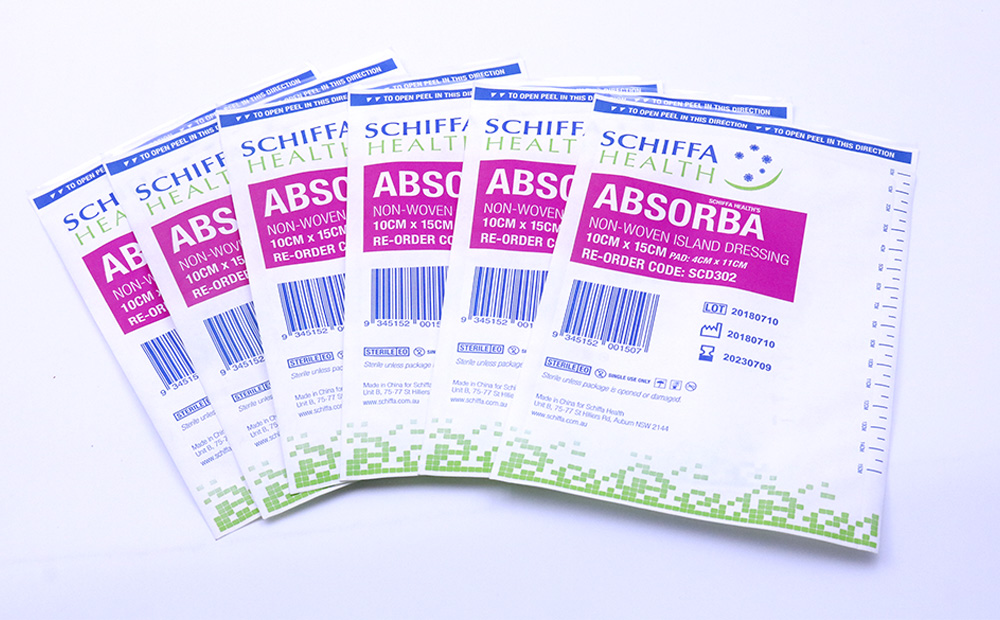
Knowing the importance of ink viscosity in the printing process, let's explore how to precisely control the viscosity of UV flexographic ink to achieve the perfect printing effect.
Using a Viscosity MeterViscosity meters are standard equipment for measuring liquid viscosity and are commonly used in the printing industry:
Rotational viscosity meters: Measure viscosity by rotating a cylinder immersed in the ink, suitable for various viscosity ranges.
Falling ball viscosity meters: Determine viscosity by measuring the descent speed of a sphere in the liquid, suitable for low-viscosity liquids.
Cup-type viscosity meters (e.g., Zahn cup, Ford cup): Determine viscosity by measuring the time it takes for a certain volume of ink to pass through a small hole, suitable for quick on-site measurements.
Temperature ControlViscosity is significantly affected by temperature, so maintaining a constant temperature for the ink and the environment is crucial:
Temperature control equipment: Use constant temperature water baths or heating plates to control the temperature of the ink.
Environmental control: Maintain a constant temperature and humidity in the printing workshop.
Thinners or AdditivesAdd thinners or thickeners to adjust the viscosity of the ink:
Thinners: Used to reduce the viscosity of the ink, but ensure compatibility with the chemical composition of the ink.
Thickeners: Used to increase the viscosity of the ink, commonly including resins or specialized additives.
Online Viscosity Control SystemSome modern printing equipment is equipped with online viscosity control systems that can monitor and adjust ink viscosity in real-time:
Sensors and controllers: Continuously monitor ink viscosity and automatically add thinners or thickeners to maintain viscosity within the set range.
Feedback control system: Automatically adjusts viscosity based on printing speed and environmental conditions.
Regular Detection and AdjustmentRegularly detect and adjust ink viscosity to ensure consistency during the printing process:
Regular sampling: Take samples from the ink tank and measure the viscosity using a viscosity meter.
Adjustment records: Record the parameters and results of each