Production process of water-based ink
Date: Aug 27 2024 From: Star Color Views:
With the increasing global awareness of environmental protection,
water-based ink, as an environmentally friendly printing material, is gradually replacing traditional solvent ink and becoming the new favorite of the printing industry. Water based ink has shown broad application prospects in various fields such as packaging printing, publication printing, and advertising printing due to its non-toxic, odorless, and easily degradable characteristics.
Many people are curious about how water-based ink is produced, and here we will explain it in detail.
Overview of raw materials for water-based inkThe raw materials of water-based ink mainly include pigments, resins, additives, and diluents.
Pigments are the basis of ink color, divided into two categories: organic pigments and inorganic pigments. When selecting, their weather resistance, dispersibility, and compatibility with resins should be considered.
Resin, as the film-forming substance of ink, has a wide variety of types, among which acrylic resin has become the most commonly used resin type in water-based ink due to its good water resistance, weather resistance, and adhesion.
Auxiliaries include wetting agents, dispersants, thickeners, defoamers, pH adjusters, etc. They play a crucial role in the fluidity, stability, and printing performance of ink.
The diluent is mainly water, and in some cases, a small amount of organic solvent may be added to adjust the viscosity and drying speed of the ink.
The manufacturing process of water-based colorantsPreliminary mixing of pigments and resinsFirstly, pre mix the pre treated pigment with some water to preliminarily disperse the pigment particles in the water. Subsequently, gradually add resin, additives, and diluents, while turning on the mixer for thorough mixing to ensure that all components are evenly mixed. During this process, attention should be paid to controlling the stirring speed and stirring time to avoid pigment particles being too large or too small, which may affect the printing effect of the ink.
Grinding and dispersionIn order to further improve the dispersion and fineness of the pigment, the preliminarily mixed pigment slurry needs to be sent to the grinding equipment for grinding. During the grinding process, the pigment particles are refined and evenly dispersed in the resin and additives. Grinding is a very important part of water-based ink production, which directly affects the quality and printing effect of water-based ink.
Filtering and Performance AdjustmentAfter grinding, the color paste needs to be filtered to remove large impurities and undissolved pigment particles.
The filtered color paste needs to be adjusted for performance according to actual needs. For example, an appropriate amount of thickener can be added to adjust the viscosity of the color paste; Add defoamers to eliminate bubbles generated during stirring and grinding processes; Adjust the pH value to ensure the stability of the color paste, etc.
Preparation and dilution of water-based inkMixing processMix the prepared color paste with film-forming resin, residual additives and other raw materials in a certain proportion to obtain water-based ink.
During the blending process, it is necessary to strictly control the proportion of each component and the stirring time to ensure the stability of the ink performance. At the same time, it is necessary to adjust the ink appropriately according to the requirements of the printing equipment and the characteristics of the printing materials.
Dilution and viscosity adjustmentIn order to meet the requirements of different printing equipment for ink viscosity, it is necessary to dilute the prepared ink. The diluent is mainly water or a small amount of organic solvent.
During the dilution process, it is necessary to gradually add diluent and stir evenly, while monitoring the viscosity changes of the ink. If necessary, the viscosity of the ink can be further adjusted by adding thickeners or adjusting the amount of diluents.
Quality Control and InspectionQuality control during the production process To ensure the stable and reliable quality of water-based ink, strict quality control is required at every stage of the production process.
This includes inspecting the quality of raw materials, monitoring the status of production equipment, controlling the production environment, and recording and tracing the production process.
Finished product inspection Finished product inspection is an important step in ensuring that the quality of water-based ink meets the standards. The inspection items include color, viscosity, fluidity, dryness, adhesion, and other aspects.
During the inspection process, professional instruments and equipment are required to test and evaluate the various performance indicators of the ink. Prevent unqualified products from entering the market.
Packaging and Storage
Packaging process During the packaging process, it is necessary to follow certain operating procedures and precautions to ensure packaging quality and safety. During the filling process, it is necessary to control the flow rate and speed to avoid the generation of bubbles and splashing; Before sealing, it is necessary to check whether the sealing of the packaging container is good.
Storage conditions Water based ink should be stored in a cool, dry, well ventilated place to avoid direct sunlight and high temperature and humidity. At the same time, it is necessary to avoid mixing with flammable and explosive materials to ensure storage safety.
During the storage process, it is necessary to regularly check the condition of the ink. If there are any abnormalities, they should be dealt with in a timely manner to avoid loss or affect subsequent use.
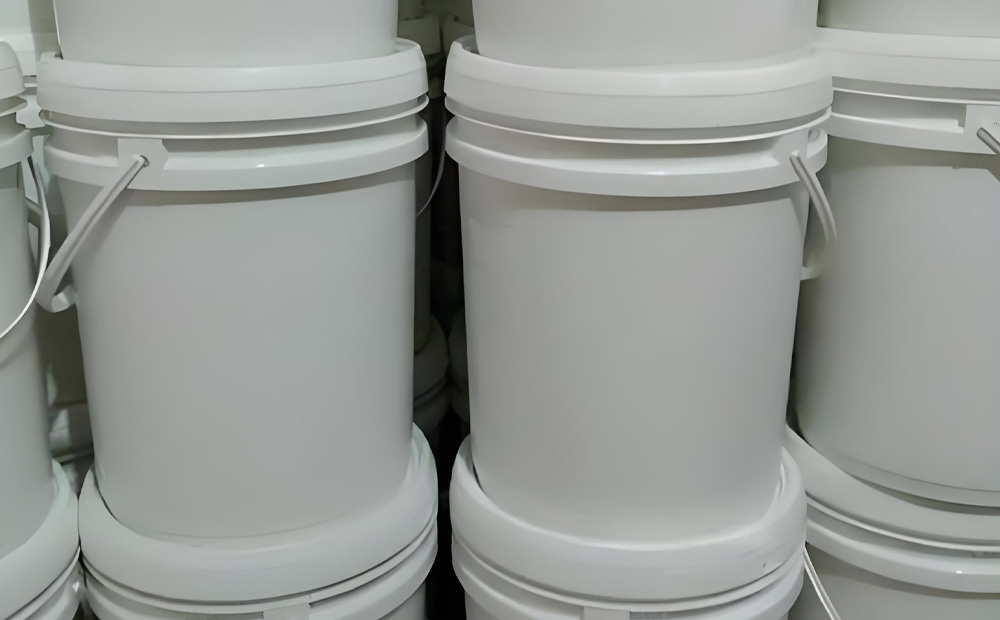
Conclusion and ProspectThe complexity and precision of water-based ink production processes reflect the modern printing industry's dual pursuit of environmental protection and quality.
With the continuous advancement of technology and increasingly strict environmental regulations, the water-based ink industry is facing unprecedented development opportunities.
In the future, water-based ink will be widely used in more fields and become the mainstream choice in the printing industry. The production process will also be continuously optimized and innovated to meet market demand and environmental requirements.
With the continuous improvement of people's awareness of environmental protection, higher requirements will be put forward for the environmental performance of water-based inks. The production process of future water-based inks still needs to focus on the research and application of environmentally friendly materials, reduce pollutant emissions during the production process, and achieve green production.