Is Water-Based Ink Safe for Printing PET Food Bags?
Date: Mar 26 2025 From: Star Color Views:
Driven by global plastic bans, PET (polyester film) has become a mainstream material for food packaging due to its high barrier properties and recyclability. According to 2024 printing industry data, water-based inks are rapidly replacing solvent-based inks for PET printing, thanks to their zero VOC emissions and non-migratory toxicity. This article provides an in-depth analysis of safe and compliant solutions for water-based ink printing on PET food packaging bags.
I. Industry Challenges and Environmental Trends in PET Food Packaging
With plastic bans implemented in 78 countries worldwide, PET now accounts for over 42% of the food packaging market. However, solvent-based inks used in PET film printing pose safety risks due to benzene residues (e.g., toluene ≤0.01mg/m²). Water-based inks are gaining traction at a 19% annual growth rate, offering environmental benefits, low VOC emissions, and food-grade compliance.
II. Four Technical Barriers and Breakthroughs for Water-Based Ink Printing on PET Food Bags
1. Adhesion Enhancement Solutions
Technical Challenge: PET has a surface energy of only 38–42mN/m, leading to insufficient penetration of water-based resins and poor adhesion (cross-cut test <3B).
Solutions:
- Corona pretreatment: Using 1.5kW power to increase the surface energy to 48–52mN/m (electrode spacing: 1.5mm).
2. Drying Efficiency Optimization
Production Pain Point: Water evaporation is 3x slower than solvent-based inks, causing over 0.1mm registration errors.
Technical Upgrades:
- Three-stage drying system:
Drying Section |
Temperature Range |
Wind Speed |
Core Function |
Infrared pre-drying |
50–60℃ |
- |
Rapid surface moisture evaporation |
Hot air main drying |
80–90℃ |
18m/s |
Deep penetration drying |
UV curing (optional) |
200mJ/cm² |
- |
Improved scratch resistance |
3. Food-Grade Safety Certification
Compliance Process:
- Migration Testing:
- Simulants: 10% ethanol (aqueous), 3% acetic acid (acidic), olive oil (fatty).
- Conditions: 40℃ ×10 days; GC-MS detected no benzene solvents.
- Heavy Metal Testing: Lead, cadmium, mercury <0.5ppm (ICP-MS method).
- Supply Chain Control: Ink suppliers must hold ISO 22000 and FSSC 22000 certifications.
4. Printing Process Adjustments
Standardized Equipment Parameters:
Equipment Type |
Anilox Roller LPI |
Ink Viscosity (Ford Cup 4) |
Printing Speed |
Gravure press |
150–200LPI |
18–22 seconds (25℃) |
150–200m/min |
Flexo press |
200–350LPI |
30–35 seconds (25℃) |
150–300m/min |
III. Comprehensive Comparison: Water-Based vs. Solvent-Based Inks
Indicator |
Water-Based Ink |
Solvent-Based Ink |
VOCs Emission |
<5% |
40%–60% |
Drying Energy |
0.9kW·h/㎡ |
0.3kW·h/㎡ (including VOC treatment) |
Water Resistance |
★★★★☆ (slight swelling) |
★★★★★ |
Safety Certification |
FDA/GB 4806.8 direct contact approval |
Requires additional exhaust treatment |
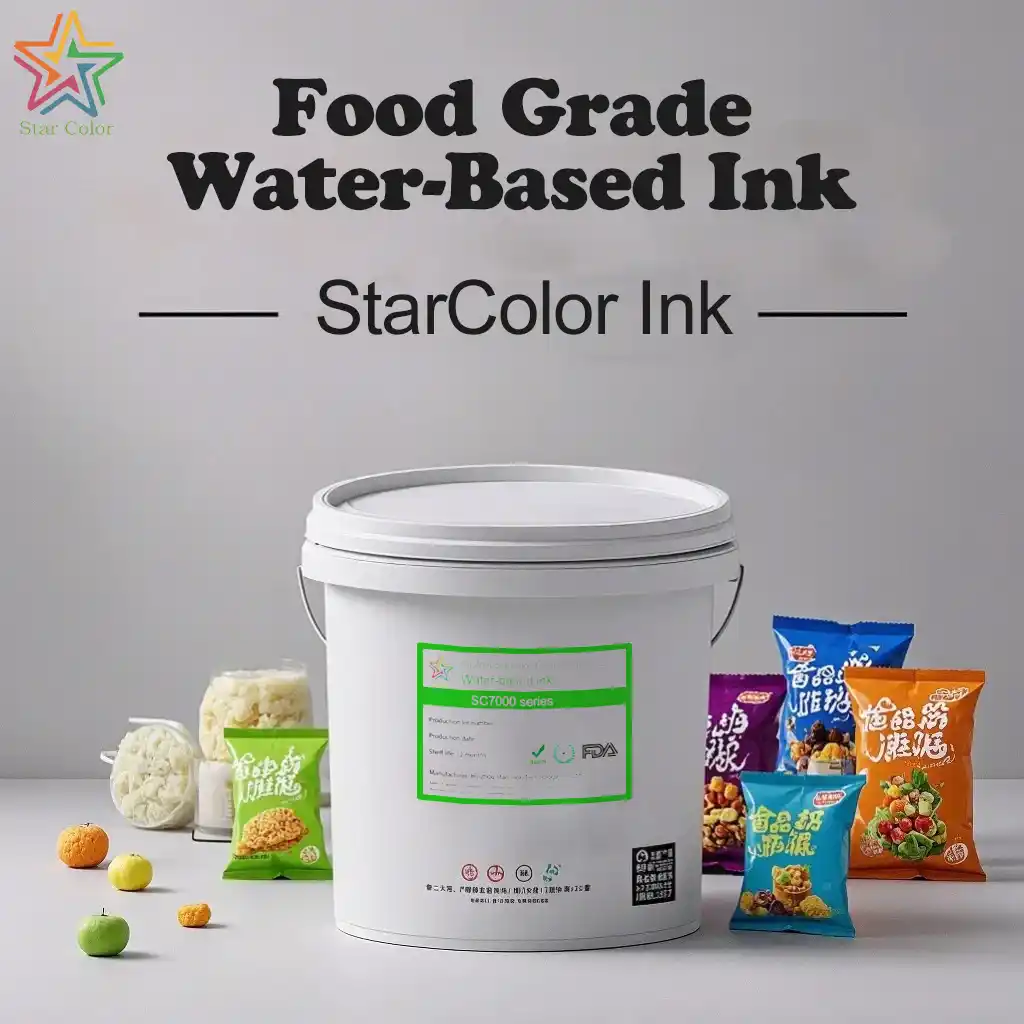
With 10 years of expertise in water-based ink R&D, Zhongzhixing is a leading provider of solutions for PET food packaging. Their SC7000 series flexo water-based inks are certified by FDA, ROHS 2.0, and REACH, offering:
- Safety: VOC emissions and heavy metals comply with national standards; olive oil migration test (40℃×10 days) showed no harmful substances.
- Printability: Viscosity of 18–22 seconds (25℃, Ford Cup 4) for high-speed flexo presses; drying speed >200m/min with ±0.05mm registration accuracy.
- Innovation: Featuring bio-based acrylic resin, the ink maintains a grade 4B adhesion rating after boiling resistance test (85℃/30min), with flex resistance exceeding 800 cycles.
Conclusion: For safe, compliant, and sustainable PET food packaging printing, water-based inks are the future. Partner with Zhongzhixing for tailored solutions that meet global standards.
If you’re seeking PET food bag printing inks, explore Zhongzhixing’s water-based solutions for a complete packaging strategy.