How to control color difference when using water-based ink printing
Date: Sep 25 2023 From: Star Color Views:
Controlling color difference when using water-based ink printing involves various factors that need to be carefully managed throughout the printing process. Water-based inks can be more sensitive to environmental conditions and substrate variations, which can affect color consistency. Here are some steps you can take to control color difference when using water-based ink printing:
1.Ink Formulation and Consistency:Ensure that your ink is properly formulated and mixed to maintain consistent color. Variations in ink formulation can lead to color differences. Always follow the manufacturer's guidelines for ink mixing.
2.Substrate Preparation:Properly prepare the substrate by ensuring it's clean, dry, and free of contaminants. The substrate's surface characteristics can impact ink absorption and color reproduction.
3.Color Management:Implement a robust color management system. This includes calibrating your monitors, using color profiles, and maintaining consistent settings across your design and printing processes.
4.Environment Control:Maintain consistent temperature and humidity levels in your printing environment. Fluctuations in temperature and humidity can impact how the ink dries and how colors appear on the substrate.
5.Testing and Proofing:Conduct regular color testing and proofing. Create test prints and proofs to ensure the desired color is achieved. Make adjustments as needed before running a full print job.
6.Press Setup:Ensure that your printing press is properly set up. Check ink rollers, blankets, and plates for cleanliness and alignment. Proper press setup contributes to consistent ink distribution and color application.
7.Ink Application:Control ink viscosity and coverage. Use a consistent ink film thickness to achieve uniform color. Be mindful of overloading or underloading the substrate with ink.
8.Drying Process:Monitor the drying process carefully. Water-based inks typically require longer drying times compared to solvent-based inks. Improper drying can lead to color shifts and smudging.
9.Operator Training:Train your operators in proper printing techniques. This includes handling the printing press, ink, and substrate to minimize variations caused by human error.
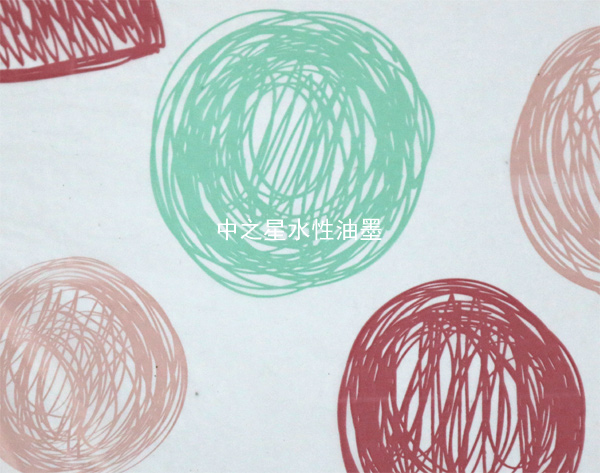
10.Batch-to-Batch Consistency:Maintain consistency across different batches of ink and substrate. Variations in the ink batch or substrate can lead to color differences.
11.Quality Control:Implement a thorough quality control process. Regularly inspect printed samples and finished products to catch any color discrepancies early and make necessary adjustments.
12.Communication with Suppliers:Maintain open communication with ink and substrate suppliers. They can provide valuable insights and support to help you achieve consistent color results.
Huizhou star color has always regarded product quality as the lifeline of the enterprise, in the production process to always monitor the production status, all links test each other, to ensure that each barrel of water-based ink is a qualified product.