Technical points of water-based ink use
Date: Oct 21 2023 From: Star Color Views:
The foam of water-based ink is mainly affected by what aspects?
The addition of wetting dispersant has obvious effect on the foam of some water-based inks.For example, polyacrylate wetting dispersants have more foams than other types of wetting dispersants.In general, wetting dispersant foam with low dispersion ability is also less.For example, diisobutylsulfonate is based on a disate, and there is little foam at its content of 0.1-0.25%.
The use of thickeners can make the defoaming of high-viscosity ink especially difficult, and this type of ink has its own special defoaming agent.The drying time of ink film is closely related to the choice of defoamer.In the printing process, the ink film is required to dry quickly, so the defoamer with strong defoaming power should be selected in the ink.
Latex inks have a high pH value.Not good for controlling bubbles.Emulsion polymer is used as film forming agent in acrylic ink, usually the particles of emulsion are very fine, which makes it difficult to work defoaming.Pigment particles such as carbon black, phthalocyanine blue and phthalocyanine green organic pigments have a tendency to increase foam in water-based inks, which is also caused by the pigment particles are too fine, and defoaming is also difficult.
Because many defoamer will affect the dispersion of the pigment, and the pigment particles will adsorb the defoamer particles, the storage stability test must be carried out when selecting the defoamer.The fillers added to the ink also affect the presence of foam, such as silica instead of talc foam will increase.However, this problem can be solved by increasing the amount of defoamer.
What are the advantages of water-based ink in the printing of plastic products?
Plastic water-based ink is composed of water-based resin, additives, pigments, water and other raw materials.In the selection of materials, all need to meet environmental requirements, in the production process all use pure water instead of organic solvents.Water-based ink is non-combustible, non-explosive, tasteless, non-toxic, is currently the world's most environmentally friendly printing ink.
Water-based ink binder is mainly divided into two types:Water dilution type and water dispersion type.There are many types of resins that can be used for the former, such as maleic acid resin, lac, maleic acid resin modified shellac, urethane, water-soluble acrylic resin, and water-based amino resin.
Water-dispersed binder is obtained by polymerization of emulsified monomer in water, it is a two-phase system, in which the oil phase is dispersed in the water phase in a granular form, although it can not be dissolved by water, but it can be diluted by water, so it can also be considered as water-in-oil emulsion.
Due to the use of water as a solvent carrier, water-based ink has significant environmental safety characteristics:Safe, non-toxic and harmless, non-combustible and non-explosive, almost no volatile organic gas generation,It is mainly manifested in the following three aspects: no environmental pollution, reduce residual poisons, reduce consumption and reduce costs.
Water-based ink commonly used additives are:1.Defoamer, used to eliminate the foam in water-based ink, the amount is generally 1% to 2%;2.Stabilizer, mainly to prevent ink in storage, transportation, agglomeration, mildew, reduce the viscosity of ink and adjust the pH value of ink, generally using ammonia or ethanolamine and other additives;3.Other additives, dispersants, preservatives, leveling agents, slippery agents and crosslinking agents, etc.Through the scientific use of these additives to improve the weakness of water-based ink, can improve the stability of water-based ink.
The solvent used in water-based ink must have:1.Dissolving resin, ink-giving;2.Adjust viscosity to give printing adaptability;3.Adjust drying rate.Water-based ink also requires non-toxic characteristics, so its solvent is mainly pure water and a small amount of alcohol, such as water, ethanol, butanol, isopropyl alcohol ,etc.These solvents can assist water to enhance the ability to dissolve resins, improve the dispersion of pigments, and accelerate penetration and inhibit foaming.
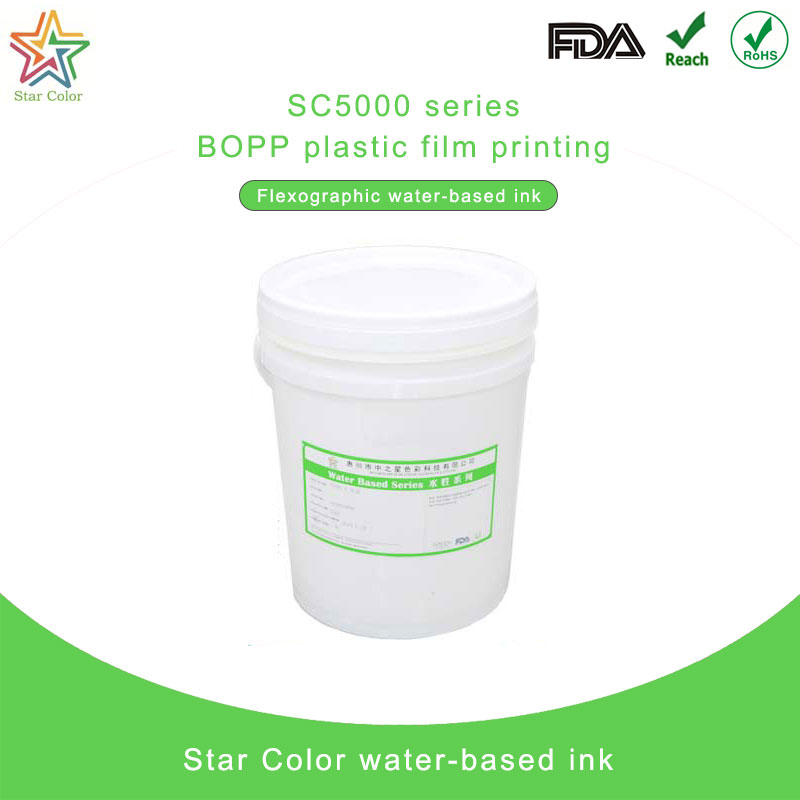
At present, the performance of water-based ink users requires improvement is:1.The application of water-based ink requires continued improvement in the application performance of polyethylene substrates;2.Alkaline resistance of water-based ink printing and packaging, and its application in frozen food packaging.The water-based ink manufacturing industry is expected to improve the surface resistance of water-based ink printing products to make more products water-based, especially in terms of oil resistance, grease resistance and better heat and freezing resistance;3.Water-based ink system with stable PH, water-based ink manufacturing industry must develop water-based ink with stable PH value in the printing process, that is, there is no need to detect and adjust PH value in printing;4.Resolubility is another important area of study, as the amine evaporates and the resin tends to cure, even on the plate.
Water-based ink printing PET film glossiness is not enough problems and solutions
The process of water-based ink printing on PET film has matured, but in actual printing, some printing companies often say that when using water-based ink to print PET film, the gloss is not enough, not as bright and bright as oily ink printing, there may be the following reasons:
1.The ink formula is not suitable
The formula of flexographic water-based ink includes a variety of ingredients such as resins, fillers, pigments, etc. If the ingredients are inappropriate or improper proportions, it may lead to low ink gloss.For example, factors such as low resin content in the ink, high filler content or low pigment opacity will affect ink gloss.
2.Improper handling of substrate
PET film surface treatment is one of the important factors affecting gloss.If the type, amount or treatment process of the substrate surface treatment agent is improper, it may reduce the gloss of the PET film surface.
3.The printing process is not appropriate
The printing process of flexographic water-based ink includes several parameters such as dot size, number of mesh lines, printing pressure, printing speed, printing temperature, etc.If these parameters are not set properly, it may lead to poor ink adhesion or uneven dispersion, which affects gloss.
4.The printing environment is unstable
The printing environment of flexographic water-based ink includes many factors such as temperature, humidity and air circulation.If the printing environment is unstable or there are contaminants, it may negatively affect the gloss of the ink.
5.Ink quality problem
If the quality of flexographic water-based ink is unqualified or there are problems, such as sediment, viscosity abnormalities, etc., it will also affect the gloss of the ink.
Improving the gloss of flexographic water-based ink on PET film can be started from the following aspects:
1.Adjust the ink formula, choose the water-based ink suitable for PET film printing, by adjusting the resin, additives, fillers and other components in the ink proportion, you can improve the gloss of the ink, do not use water-based ink printing other materials to print PET substrate.
2.Select the appropriate printing process, in the printing process, reasonable control of the printing machine printing speed, pressure, temperature and other parameters, as well as the selection of the appropriate mesh line number and dot size and other printing process, can improve the gloss of the print.
3.Optimize the surface treatment of the substrate and select the appropriate coating process.In the printing process, the coating polishing process can be used, and the gloss of the print can be increased by coating the surface of the print after printing.