How to solve the problem of water-based ink in the printing process
Date: Oct 27 2023 From: Star Color Views:
With the continuous development of flexographic printing machines, the demand for water-based inks and various new flexible inks in the packaging and printing industry will be more urgent, and the demand will be further increased.At present, there are nearly 1,000 flexo printing machines for various types of cartons in China, mainly using water-based ink printing, with an annual consumption of more than 50,000 tons, accounting for 25% of the total ink consumption.
There are two reasons why ink is suitable for carton printing:
一. Because the corrugated cardboard is a loose interwoven fiber, strong water absorption, water-based ink transferred to the surface of the cardboard is easy to penetrate and dry, there is no need to set a drying device;
二.Because water-based ink is non-toxic, harmless, non-flammable, safe and convenient to use, low cost.
1.Composition of water-based ink
Water-based ink is made of water-based polymer resin and emulsion, organic pigment, water solvent and related additives mixed by physical and chemical process, does not contain volatile organic solvent, does not contain some toxic and harmful substances in solvent ink.Its environmental protection is more suitable for food, beverage, medicine and other products with strict health requirements.
Color is the coloring substance of ink, choose more organic pigments with complete chromatography, high color concentration and easy to achieve high hiding power, such as magenta ink, yellow ink, green ink and other organic pigments are generally used;White ink multi-purpose titanium dioxide; Black ink is carbon black.
Water-soluble or water-dispersed resin is the ink binder, is an important factor affecting the quality of ink, viscosity, adhesion, gloss, drying and other printability depends on the composition of the resin.At present, the research and development of ink by domestic ink companies mainly focuses on the research of binder, including water-soluble binder based on polyvinyl alcohol, hydroxyethyl cellulose and polyethylpyrrolidone, saline-alkali soluble binder of soluble resin and diffusion binder commonly known as latex containing propylene, ethylene or butadiene polymer.
From a formula perspective, the ability of domestic ink mixing oil packaging pigment printing paste is poor, only reaching 50%, while the ability of imported resin packaging color paste reaches 80%.Domestic ink due to coarse particle size, easy to damage the printing roller, imported ink particle size is finer, with the roller to form a good affinity, will not scratch the surface of the printing material and affect the printing effect.
The additives of water-based ink include amine stabilizer, defoamer and slow drying agent, which are used to adjust PH value, eliminate bubbles and adjust curing drying time, etc.Color and ink mixing oil are important raw materials for ink manufacturing. We use imported color paste and ink mixing oil in our domestic ink mixing.
When selecting water-based ink, attention should be paid to the viscosity, concentration, fineness, drying speed, wear resistance, water resistance and stability of the ink.
2.Factors affecting the viscosity of water-based ink
Viscosity is the size of ink cohesion, and it is also the most important control index in ink and wash applications.The viscosity of ink is too low, which can cause drawbacks such as light color, large dot expansion, deformation of highlights, and uneven ink transfer;The viscosity of ink is too high, it will affect the ink transfer performance of the mesh roller, the ink color is uneven, the color is sometimes not deep, and it is easy to cause dirty version, paste version, foaming, dry and other ills.
Temperature
The viscosity is most sensitive when the temperature difference is large in winter and summer.When the temperature is high, the water evaporates quickly and dries quickly. During operation, it is necessary to pay attention to extending the drying time or improving the machine speed;When the temperature is low, the water evaporates slowly, and the ink drying is also slow. During operation, the drying speed of the ink can be increased or the drying device can be added.
When used in winter, because the ink is easy to freeze below 0 ° C, if the ink is frozen, it can be placed in a room with a high temperature, let it dissolve naturally, and can continue to use after mixing evenly.
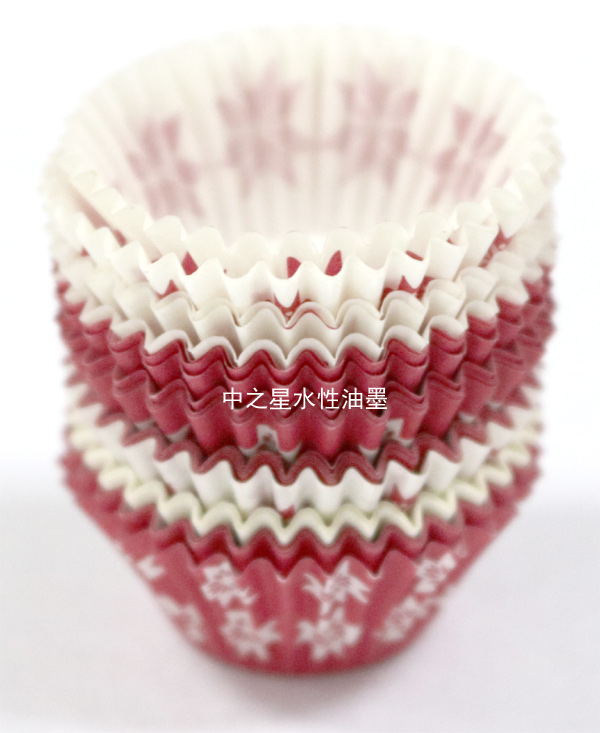
In actual production, when using a press with an ink scraper, the amount of ink transfer when the temperature is too low is not as stable as when the temperature is slightly higher. The increase in the temperature of the ink will reduce the viscosity, and the result is a reduction in the density of the print and a thinning of the ink layer.To maintain the consistency of printing quality, it is necessary to maintain the consistency of ink viscosity.
The printer must attach great importance to the impact of the ink temperature, and the temperature of the ink should be stabilized at the temperature of the printing workshop before printing.This measure is very important, otherwise the ink density in the printing process will have a significant change.
Thixotropy
Thixotropy means that the fluidity of the ink increases under the action of external agitation, and the fluidity gradually decreases after the agitation is stopped and the performance of the original state is restored.After the ink is placed for a long time, some ink with poor stability is easy to precipitate and layer.There are also false thickening phenomena.At this time, it can be fully stirred, and after a certain time of stirring, the above problems will disappear naturally.
When using fresh ink, be sure to mix well in advance and then make dilution adjustment.Or it is expected that after a certain amount of ink is applied to the machine, the viscosity will decrease, because the water content in the machine and the thixotropy of the ink can improve the fluidity of the ink.When printing is normal, it is also necessary to regularly stir the ink, especially the ink with high white pulp content.
The PH of the ink
The PH value of another indicator that needs to be controlled in ink application, and its normal range is 8.5~9.5, then the printing performance of water-based ink is the best and the quality of printing is the most stable.Because ammonia is volatile in the printing process, the operator will also add new ink and various additives to the ink from time to time, so the PH value of the ink may change at any time.
Using a standard PH meter, you can easily measure the PH value of the ink.When the PH value is higher than 9.5, the alkaline is too strong, the viscosity of the water-based ink is reduced, the drying speed is slow, the water resistance is poor, and easy to paste.When the pH value is below 8.5, i.e. the alkalinity is too weak, the viscosity of water-based ink will increase, making the ink easy to dry and blocking the plate and anilox roller, causing dirt on the plate and generating bubbles.The influence of PH value on the printability of water-based ink is mainly manifested in the viscosity stability and dryness of ink and the clarity of dot.With the increase of PH value, the viscosity of ink decreases and the drying speed slows down.
Water-based ink application experience
Water-based ink often encounters some problems in the process of cardboard printing, and the cause analysis and solution can be referred to as follows:
The adjustment of the printing pressure is critical, which includes the pressure between the plate and the substrate and the pressure between the roller and the plate.If the ink viscosity is too high, ink drying too fast, the solution is to adjust the pressure, dilute the ink, add slow drying agent.
If the ink is dry on the printing plate, the printing edge is fuzzy, it may be hot air blowing on the printing plate, and the paper fiber mixed with the ink leads to electrostatic reaction. The elimination method is to dilute the ink and gradually increase the speed, cover the inking system, or replace the ink and install the electrostatic device.
Flexographic is especially suitable for field printing, if the field is not real, the cause may be the ink viscosity is too low, the substrate surface is uneven, the solution is to use high viscosity ink, the use of good surface quality substrate material.
The ink is piled up on the plate or the dot is piled up, the reasons include too much ink, too much printing pressure, ink drying too fast or ink is too weak, etc. The solution is to replace the anilox roller, adjust the pressure, add slow drying agent or use high color strong ink.
The reasons for the poor printing adhesion are too low ink drying temperature, ink and material no affinity, material surface Dyne value is too low need corona treatment, the solution is to measure the surface tension, increase the drying temperature, replace the ink variety or make the surface of the substrate.