How to use water-based ink additives do you really know
Date: Nov 22 2023 From: Star Color Views:
We know that water-based ink is mainly composed of water-soluble resins, pigments, water and auxilaries.In the process of using water-based ink, it is often necessary to add some additives to change the properties of the ink to achieve the best printing effect,It can be said that the use of additives is directly related to the printing quality of water-based ink,Therefore, the use of additives is very critical, and to know how to use additives, we first have to talk about the characteristics of these additives.
1.Pigment is used to deepen the color, and its dosage should generally be controlled in the range of 0 to 30%, more than 30% will make the connection content in the ink is too low, resulting in a decrease in its adhesion and wear resistance.
2.The PH stabilizer is used to adjust and control the pH value of the water-based ink, so that it is stable at 8.0 ~ 9.5, and ensure the printing state of the water-based ink.At the same time, it can also adjust the viscosity of water-based ink and dilute the ink.
3.Slow drying agent is used to reduce the drying degree of ink, slow drying agent can inhibit and slow down the drying speed of water-based ink, prevent ink from drying on the plate, and reduce the occurrence of printing failures such as blocking and paste plate.The amount of slow drying agent should generally be controlled at 0 to 10% of the total amount of ink, if the amount is added too much, the ink drying is not thorough, the print will stick dirty or produce odor.
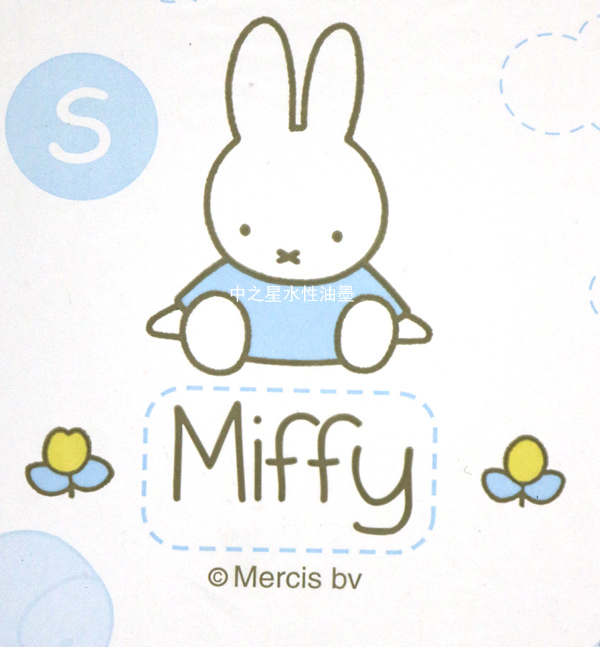
4.The diluent is a milky, pulpy liquid with a certain viscosity and a high PH value,It can adjust various colors and dilute four-color inks without reducing viscosity and PH value, and can be used directly on the machine to enhance the brightness of printed products.The dosage can be determined based on the user's color draft and the depth of the color.
5.Diluent, the additive is mainly used to reduce the viscosity of ink,The dosage should be controlled within 3% to avoid reducing the color depth of the ink and maintain the pH value of the ink.The thinner should be added slowly while stirring to prevent the viscosity from being too low.If the addition of more diluent or the use of high hardness of tap water dilution will produce bubbles, then the defoamer should be added.
6.Defoaming agent,The main performance of defoamer is to eliminate bubbles in water-based ink and prevent problems such as white spots, sand holes and water marks caused by bubbles in printing.The amount is generally 0.5% ~ 1%, the amount is too much, but it affects the quality of the product, it is best to spray from the sprayer.
7.Blocking agent,Blocker agent is a slightly yellowish liquid with a PH value of about 5.5, which can inhibit and reduce the curing and drying time of water-based ink,To prevent the surface crust, the speed is too slow and the water-based ink drying too fast caused by dirty plate, paste plate phenomenon has a certain inhibitory effect.When the viscosity of water-based ink is too large, and there is no need to use excessive blockers, it can be used after diluting with water, and the general dosage is controlled at 3% to 5%.
These are some of the additives we often use in the use of water-based ink and their characteristics, additives are an important component of water-based ink,Only when we clearly know the characteristics and usage of these additives can we achieve the best effect of water-based ink in printing.