How to improve the abrasion resistance of UV water-based ink
Date: Feb 20 2024 From: Star Color Views:
With the continuous development of the printing industry, the demand for ink friction resistance is also getting higher and higher.UV water-based ink as a kind of environmental protection, fast drying ink, its friction resistance still needs to be improved.This paper aims to discuss how to improve the abrasion resistance of UV water-based ink, and provide guidance for practical production through experiment and theoretical analysis.
With the wide application of printed matter in daily life, the quality and durability of printed matter are increasingly demanded.UV water-based ink, as a new type of environmental protection ink, although to a certain extent to meet people's needs for fast drying, low VOCs, but its friction resistance is still a problem to be overcome.This paper will deeply discuss how to improve the abrasion resistance of UV water-based ink.
Factors affecting friction resistance
Resin composition: Resin is the main film forming substance in the ink, and its properties determine the final performance of the ink.Choosing the right resin is very important to improve the friction resistance.
Fillers and pigments: Certain fillers and pigments can enhance the friction resistance of the ink.For example, some high-hardness inorganic fillers and pigments with a high refractive index can enhance the gloss and hardness of the ink surface.
Additives: An appropriate amount of plasticizers, leveling agents and other functional additives can effectively improve the friction resistance of the ink.
Curing conditions: The power of the UV lamp, irradiation time and distance will affect the degree of curing of the ink, thus affecting the friction resistance.
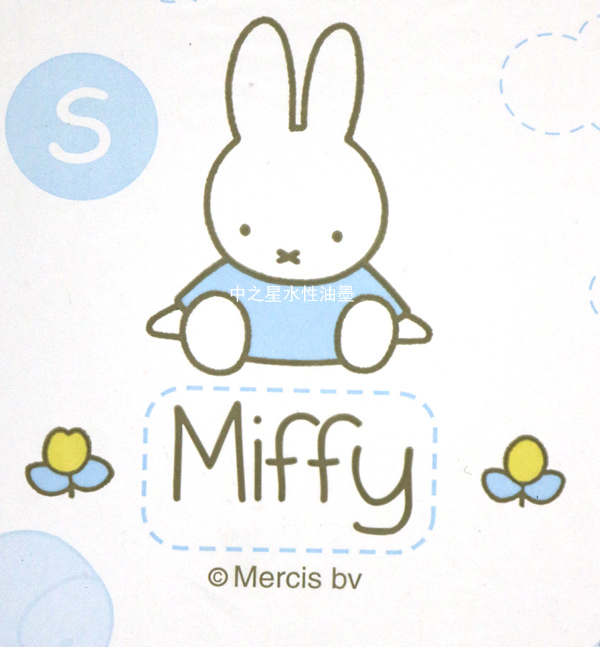
Methods for improving friction resistance
Choose the right resin: The use of high hardness, high durability of the resin can significantly improve the friction resistance of the ink.For example, epoxy resin, polyurethane resin, etc., have better durability.
Optimize the ratio of fillers and pigments: Adjust the ratio of fillers and pigments according to actual needs to achieve the best anti-friction effect.
The use of additives: the appropriate amount of plasticizer can increase the flexibility of the ink and improve its anti-friction ability;The addition of leveling agent can improve the surface smoothness of the ink and reduce friction resistance.
Optimize curing conditions: By adjusting the power of the UV lamp, irradiation time and distance, ensure that the ink is fully cured to achieve the best friction resistance.
Surface coating treatment: Coating a layer of wear-resistant coating on the surface of the ink, such as UV coating or wear-resistant wax, can effectively improve the friction resistance of the ink.
Process improvement: By improving the printing process, such as controlling the printing pressure, optimizing the drying conditions, etc., the friction resistance of the ink can also be improved to a certain extent.
Formula optimization: Continue to optimize the ink formula, through a large number of experiments and tests, to find the best formula ratio to improve friction resistance.
Post-treatment process: After the printing is completed, appropriate post-treatment, such as heating, pressure, etc., helps to improve the adhesion between the ink and the substrate material, thereby improving the friction resistance.
Application of nanotechnology: The use of nano-materials such as nano-fillers and nano-modifiers to modify ink can significantly improve its friction resistance.
Research and development of new UV water-based ink: For the anti-friction performance of special research and development work, the development of a new UV water-based ink with excellent friction resistance.
The above method can effectively improve the friction resistance of UV water-based ink, and provide more durable and better quality prints for the printing industry.At the same time, these methods also provide ideas and directions for the further development and improvement of UV water-based ink.It is hoped that this paper can provide some reference and help for technical personnel and R&D personnel in the printing industry.