Detailed explanation of water-based ink
Date: Jul 24 2024 From: Star Color Views:
1、 Introduction
Water based ink is a printing ink system that uses water as the main solvent or dispersion medium. It abandons the extensive use of organic solvents in traditional solvent based inks and instead uses water-soluble resins as connecting agents, supplemented with organic pigments, functional solvents (such as water, small amounts of alcohols or ethers to adjust viscosity, drying speed, etc.), and various necessary additives, processed through grinding technology. This unique formula not only gives water-based inks environmental advantages that solvent inks cannot match, but also ensures that printing speed, effect, color, and glossiness are not inferior.
Driven by the wave of global environmental protection, the demand for sustainable development and green production in various industries is becoming increasingly urgent. The printing industry, as an important component of traditional manufacturing, has long been concerned about the pollution problems generated during its production process. Traditional solvent based inks contain a large amount of volatile organic compounds (VOCs), which can easily release harmful gases during printing, drying, and waste disposal processes, posing a threat to the environment and human health. Therefore, seeking and promoting alternative products to reduce VOCs emissions has become an inevitable choice for the transformation and upgrading of the printing industry.
The production of water-based ink has been rapidly applied in various fields such as packaging printing, commercial printing, and publication printing due to its low VOC emissions, good printing adaptability, easy to clean printing equipment, and shorter drying time. From an environmental perspective, water-based ink can significantly reduce the emission of air pollutants, improve air quality, and protect the ecological environment; From an economic perspective, although the initial investment may be slightly higher than that of solvent based ink, in the long run, its low energy consumption and low emissions characteristics help companies save environmental treatment costs, enhance brand image, and strengthen market competitiveness.
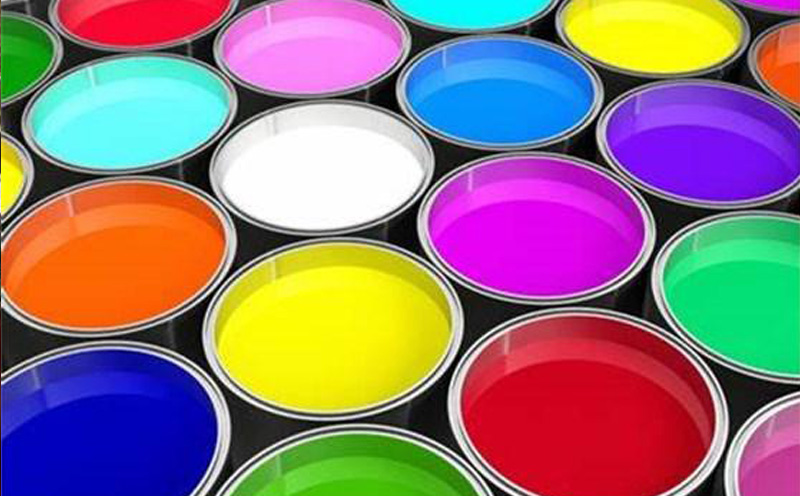
In addition, water-based ink also has excellent color reproduction ability and printing stability, which can meet the modern printing industry's demand for high precision, high speed, and high quality. With the continuous advancement of technology and further cost reduction, the application scope of water-based ink will continue to expand, promoting the entire printing industry to develop towards a greener, more efficient, and sustainable direction.
2、 The development of water-based ink
At the beginning of the 20th century, with the acceleration of industrialization, the printing industry experienced rapid development. However, the emission of volatile organic compounds (VOCs) in traditional solvent based inks has gradually attracted global attention. In this context, scientists have begun to explore more environmentally friendly ink alternatives, and the concept of water-based ink has emerged. In the early stages, due to technical limitations, the performance of water-based inks was not yet stable and their application scope was limited. They were mainly used in fields where environmental requirements were not particularly high.
In the mid to late 20th century, with the rapid development of science and technology, water-based inks experienced significant technological breakthroughs. Developed countries such as Europe and North America have taken the lead in increasing investment in the research and development of water-based inks. By introducing new resins and improving production processes, key performance indicators such as water resistance, glossiness, and drying speed of water-based inks have been significantly improved.
In the 21st century, with the increasingly strict global environmental regulations, the application of water-based inks has rapidly expanded worldwide. In various fields such as packaging printing, commercial printing, and publication printing, water-based inks have gradually replaced some traditional solvent based inks due to their environmental, safety, and economic advantages. Especially in developed countries such as Europe and the United States, water-based ink has become the mainstream choice for packaging printing.
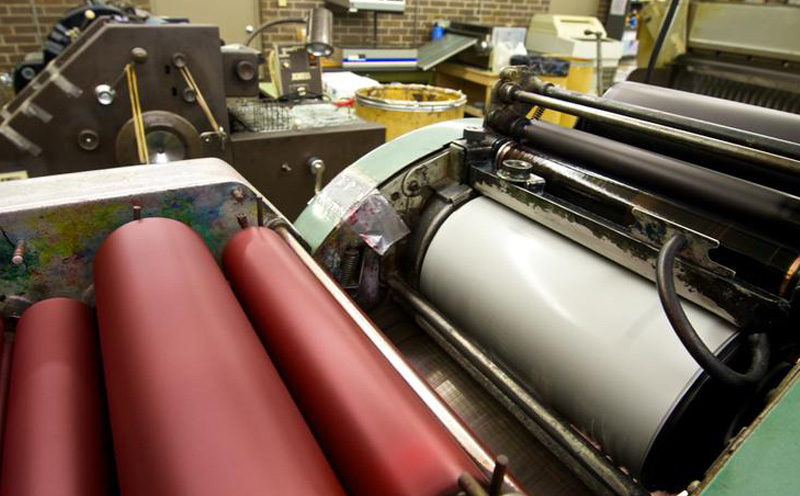
At the same time, developing countries have also begun to attach importance to the application and promotion of water-based inks. With the awakening of environmental awareness and the continuous progress of printing technology, more and more developing countries are introducing water-based ink technology to meet domestic market demand and enhance international competitiveness. This trend has driven the popularization and development of water-based inks worldwide.
3、 The main components of water-based ink
Water soluble resin: As a binder, it has a significant impact on the viscosity, adhesion, gloss, drying, and printing adaptability of ink. Common types include maleic acid resin, water-soluble acrylic resin, polyurethane resin, etc.
Pigments: To give ink color, alkaline resistant pigments should be selected.
Solvent: mainly water, a small amount of alcohol and other auxiliary solvents.
Additives: including defoamers, stabilizers, slow drying agents, etc., used to improve the specific printing performance of ink.
4. Production process of water-based ink
4.1 Raw material selection and preparation
The main raw materials for water-based ink include pigments, resins, additives, diluents, and water.
Pigments: Pigments are an important component of water-based inks, giving them color. Pigments can be organic or inorganic pigments, commonly including phthalocyanine blue, ketone acid blue, iron oxide, chromium oxide, etc. The selection of pigments should consider their color, coloring power, covering power, dispersibility, and wear resistance.
Resin: Resin is the main curing agent for water-based ink and also the connecting material for ink. It evenly disperses pigment particles and endows ink with certain fluidity, adhesion, and drying speed. Commonly used resins include acrylic resin, polyurethane resin, etc.
Additive: Additive is an auxiliary component of ink used to improve specific properties of ink. Common additives include pH stabilizers, defoamers, fast drying agents, slow drying agents, diluents, thickeners, etc.
Diluents: Diluents are mainly used to adjust the viscosity and fluidity of ink, and commonly used diluents include water and a small amount of ethanol.
4.2 Production process flow
The production process of water-based ink usually includes the following steps:
Premixing of pigments with water: Mix and stir the pigments with a certain amount of water to disperse them evenly and form a slurry like pigment body. This step is the initial stage of pigment dispersion.
Adding resin and additives: Add resin, additives, and diluent to the pigment premix and stir thoroughly. The purpose of stirring is to thoroughly mix the resin and additives with the pigment to form a uniform ink system.
Grinding: Grind the prepared ink. The purpose of grinding is to refine pigment particles and improve the color saturation and glossiness of ink. By friction, pigment particles become finer. After the introduction of new equipment by Huizhou StarColor, the fineness of grinding can reach the nanometer level.
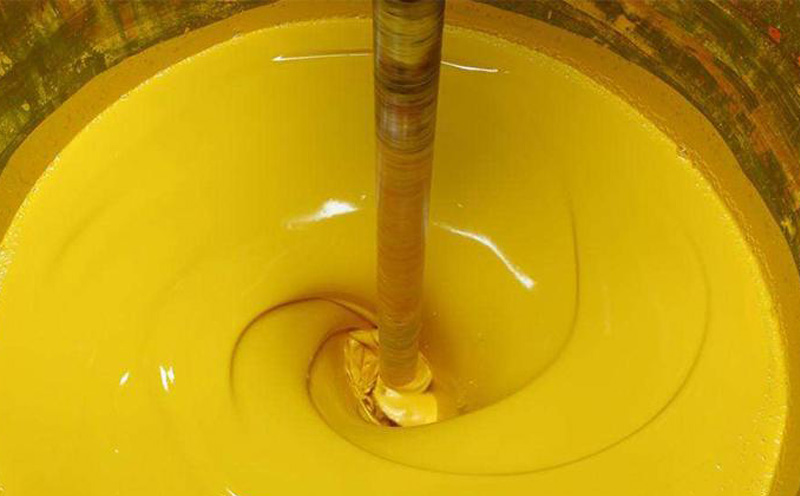
Filtering treatment: The ink after grinding needs to be filtered to remove impurities and particles. The selection of filters should be based on the requirements of the ink to determine the appropriate pore size. The filtered ink is purer, which is beneficial for improving printing quality and stability.
Adjusting viscosity and performance: According to the requirements of ink use, adjust the viscosity of the ink by adding additives such as diluents or thickeners. At the same time, other additives can be added as needed to improve the flowability, dryness, and other properties of the ink. Huizhou StarColor has always adopted a high concentration and low viscosity approach, greatly enhancing the ink's coverage.
Packaging and Storage: Pack and store the prepared water-based ink properly. The packaging form can be selected according to the purpose of the ink and customer needs, with appropriate packaging materials and specifications. Attention should be paid to controlling temperature and humidity conditions during storage to prevent ink deterioration or performance degradation.
5. Characteristics of water-based ink
5.1 Environmental friendliness
Low VOC emissions: The solvent of water-based ink is mainly water and a small amount of alcohols, which significantly reduces the emission of volatile organic compounds (VOCs) and helps to reduce pollution to the atmospheric environment.
Non toxic and harmless: Compared with solvent based ink, water-based ink is non-toxic, non corrosive, and has no irritating odor, which is harmless to workers' health. It is particularly suitable for packaging printing that requires high hygiene standards, such as food and medicine.
5.2 Safety
Non flammable and non explosive: Water based ink is non flammable and non explosive, greatly reducing fire hazards and improving production safety.
Reduce static electricity and fire risk: As the solvent of water-based ink is mainly water, it is not easy to generate static electricity, thereby reducing the risk of fire caused by static electricity.
5.3 Printing Performance
High color density: Water based ink has a high color density, which can present bright and full color effects.
Strong printability: Water based ink has good fluidity and is easy to uniformly adhere to printing surfaces of various materials, suitable for multiple printing methods.
Fast drying: Water based ink has a moderate drying speed, which is beneficial for improving printing efficiency.
5.4 Operability
Easy to operate: When printing, simply add tap water and prepare the ink in advance. During the printing process, simply add an appropriate amount of new ink, making the operation simple.
Good stability: Water based ink has good stability, is not easy to layer or clump, and is conducive to maintaining stable printing quality.
5.5 Economy
Low overall cost: Although the unit price of water-based ink may be slightly higher than that of solvent based ink, due to its solvent being mainly water and high color concentration, the depth of gravure printing can be relatively shallow, resulting in lower overall usage costs. In addition, with the depletion of petroleum resources and the rise in organic solvent prices, the manufacturing and environmental costs of solvent based inks will continue to increase, while the economic advantages of water-based inks will become more apparent.
5.6 Other characteristics
Water resistance: Water based ink has good water resistance after drying and is not easily eroded or dissolved by water.
Weather resistance: Some high-end water-based inks also have good weather resistance and can maintain bright colors for a long time in outdoor environments.
6. Application areas of water-based ink
6.1 Printing of Paper Products (Absorbent Materials)
Various types of paper, such as kraft paper, copperplate paper, thermal paper, glassine paper, release paper, and corrugated cardboard. After being printed with water-based ink, these papers can be used to make common products such as cardboard boxes, paper bags, and adhesive paper.
Food grade paper products: The application of water-based ink is particularly important for food grade paper products such as paper trays, paper cups, napkins, and paper straws. Due to its environmentally friendly and non-toxic characteristics, it can meet the high requirements for hygiene and safety in food packaging.
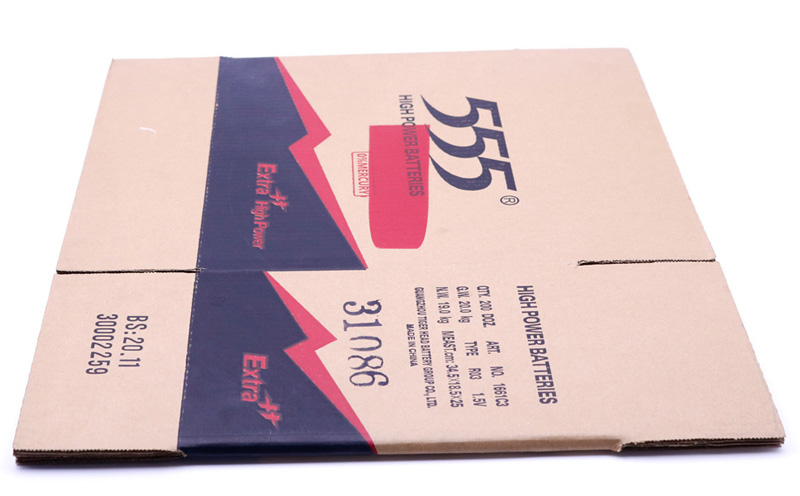
6.2 Printing of Plastic Products (Non Absorbent Materials)
Plastic woven products: LDPE, HDPE, PP and other woven materials are common plastic woven materials. After printing with water-based ink, they can be made into woven bag products such as cement bags, feed bags, container bags, and flour bags.
Plastic film products: Non absorbent materials such as LDPE, HDPE, BOPP, PVC, PET, and PO can also be printed using water-based ink. These film materials are widely used in plastic packaging products such as vest bags, clothing bags, garbage bags, express bags, and chemical bags, as well as food grade products such as diapers, sanitary napkins, and snack bags.
7. Printing method of water-based ink
There are various printing methods for water-based ink, mainly classified according to the type of printing plate or printing method. The following are several common printing methods for water-based inks:
7.1 letterpress printing
Convex printing is a printing method in which the ink covered part of the printing plate protrudes from the non ink covered part. Toppan ink is mainly used for printing books, magazines, newspapers, picture books, documents, account books, etc.
Relief ink is further divided into lead printing ink, copperplate ink, relief rotary ink, flexible relief ink, etc. according to the type of printing machine and the purpose of the printed product.
7.2 Flexographic Printing
Flexographic printing is a method of printing using flexible printing materials, and flexographic printing is also a type of relief printing. Its ink usually has good fluidity and transferability to adapt to the printing characteristics of flexographic printing materials. Currently, flexographic printing is the most commonly used printing method for water-based ink.
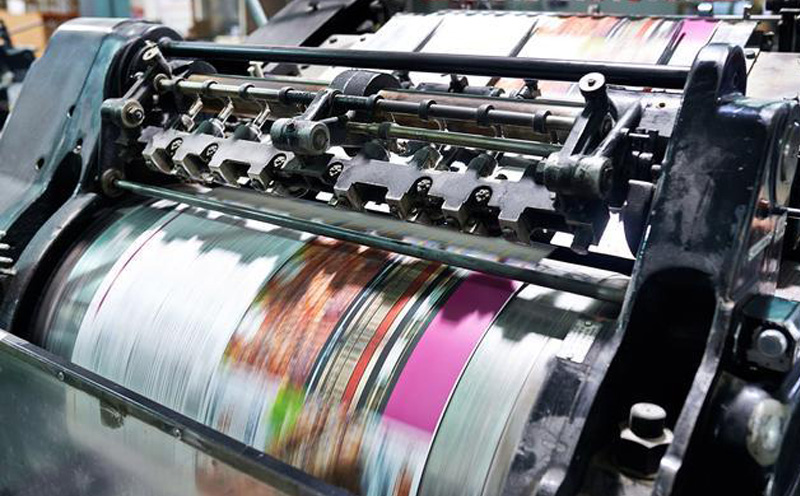
Flexographic printing occupies an important position in the field of packaging printing, especially widely used in the printing of corrugated cardboard boxes, plastic bags, labels and other products.
7.3 gravure printing
During gravure printing, ink is applied to the pattern areas that are recessed into the layout, and the ink on non pattern areas is wiped off or scraped off before printing. Gravure ink is divided into engraved gravure ink and photographic gravure ink.
Gravure ink is widely used in the field of packaging printing, such as printing on plastic films, paper, aluminum foil, etc., especially on high-quality printed products such as cigarette packs, wine boxes, and food packaging boxes.
7.4 Screen Printing
During screen printing, ink leaks through the mesh holes of the printing plate onto the printing surface for printing. More suitable for printing molded items,
Screen printing has the characteristics of thick ink layer, strong three-dimensional effect, and wide printing adaptability. It is widely used in the printing of various materials such as glass, ceramics, metals, plastics, and paper, especially in the fields of electronic products, handicrafts, advertising signs, etc.
8. The current development status of water-based ink
The global water-based ink market continues to expand in size. The global water-based ink market size reached 22.015 billion yuan in 2023, and is expected to grow at a compound annual growth rate of 5.34% to 30.61 billion yuan by 2029.
North America and Europe are important consumer regions for water-based inks worldwide, with a high market share. Meanwhile, Asian countries such as China and Japan also hold significant market shares.
The development trend of water-based ink
Environmental Protection:
With the increasingly strict environmental regulations and the improvement of consumer environmental awareness, water-based ink, as a representative of environmentally friendly ink, has a very promising market prospect. In the future, the water-based ink industry will continue to develop towards a more environmentally friendly and low pollution direction.
High quality:
Water based ink not only needs to meet environmental standards, but also needs to have good printing effects and quality. In the future, the research and development of water-based inks will pay more attention to improving printing effects, including color vividness, adhesion, light resistance, and other aspects.
Intelligence and digitalization:
With the continuous development of artificial intelligence technology, the production method of water-based ink will also move towards intelligence and digitization. The automation, digitization, and intelligence of the production process through information technology will improve production efficiency and quality.
diversification:
The application fields of water-based ink are constantly expanding. In the future, water-based inks will be involved in printing needs in more fields such as automotive, construction, electronics, and other industries. At the same time, with the continuous emergence of new materials and technologies, more application scenarios will be created for water-based inks.
9. Summary
Water based ink, as an important environmentally friendly material in the printing industry, has received widespread attention and application worldwide in recent years. From the perspective of global development status, water-based ink not only conforms to the trend of environmental protection, but also has achieved significant achievements in technological innovation and market expansion.
Developed countries and regions such as North America and Europe, as important consumer areas for water-based inks, continue to expand their market size and consumer demand. Internationally renowned ink companies have increased their investment in the field of water-based ink, continuously improving the competitiveness and market share of their products through technological innovation and product development. Meanwhile, with the increasing global awareness of environmental protection and the improvement of regulations, water-based ink, as a representative of environmentally friendly ink, has a very broad market prospect.
From the perspective of development trends, water-based inks will continue to develop towards environmental friendliness, high quality, intelligence, and diversification. Firstly, environmental protection is the primary trend in the development of water-based inks. With the increasingly strict environmental regulations and the improvement of consumer environmental awareness, water-based inks will pay more attention to improving their environmental performance, reducing VOCs emissions, and minimizing environmental pollution. Secondly, high quality is the core direction of the development of water-based inks. In the future, water-based inks will continuously improve printing effects and quality, meeting the market's demand for high-quality printed materials.
Meanwhile, intelligence and digitization will also become important trends in the development of
water-based inks. The automation, digitization, and intelligence of the production process through information technology will improve production efficiency and quality, and reduce production costs. Finally, diversification is an inevitable trend in the development of water-based inks. With the continuous emergence of new materials and technologies, water-based inks will be involved in more fields of application, such as the printing needs of industries such as automotive, construction, and electronics, creating more market opportunities for water-based inks.