The Importance of UV Ink Viscosity
Date: Jul 29 2024 From: Star Color Views:
UV ink is a relatively special type of printing ink that achieves rapid curing through the irradiation of ultraviolet (UV) light. The main components of UV ink include resin, pigment, photoinitiator, additives, etc. When these components are mixed in specific proportions, they form a liquid material that can react quickly under UV irradiation.
Due to the minimal solvent evaporation during the curing process of UV ink, its impact on the environment is relatively small and meets environmental requirements.
To print good printed products using UV ink, it is necessary to control the viscosity of UV ink, otherwise it will be difficult to demonstrate the advantages of UV ink,
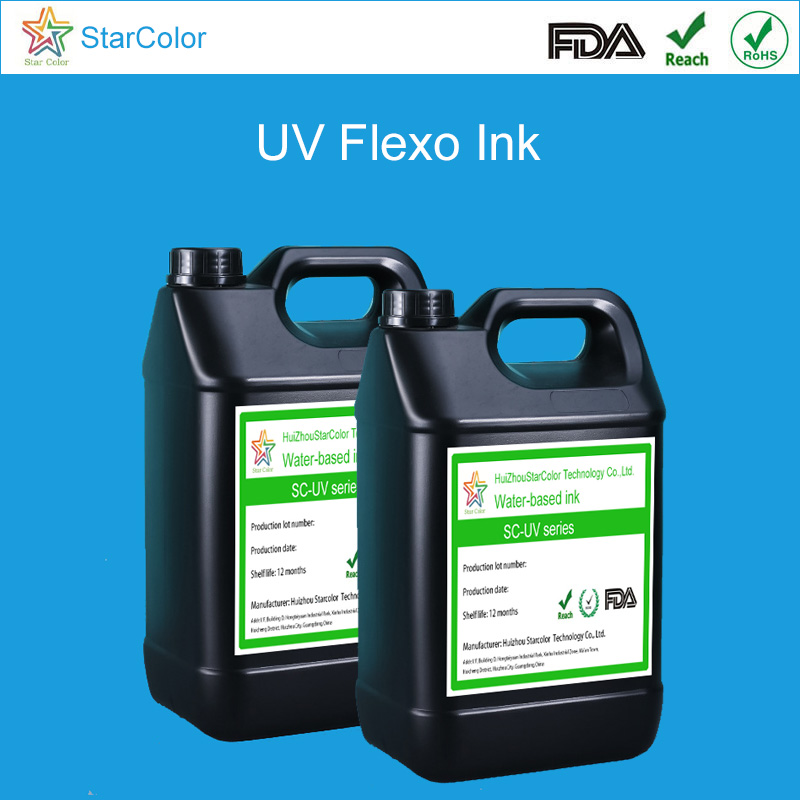
The viscosity of UV ink has a crucial impact on printing quality, mainly reflected in the following aspects:
1. Ink transfer and printing uniformity
Viscosity and transfer rate: Viscosity is a key factor determining the transfer rate of UV ink. When the viscosity is too high, the ink is difficult to transfer evenly from the printing plate or ink roller to the substrate, resulting in unclear and uneven printing patterns, and even leakage. On the contrary, low viscosity may cause ink to permeate or diffuse during the transfer process, affecting the precision and clarity of printed materials.
Liquidity: Appropriate viscosity helps ink maintain good fluidity during the printing process, ensuring that the ink can smoothly pass through the printing equipment and evenly adhere to the substrate.
2. Glossiness and color saturation of printed materials
Glossiness: The viscosity of UV ink directly affects the glossiness of the printed surface. Ink with moderate viscosity can form a smooth and shiny ink film after curing, enhancing the glossiness and visual effect of printed materials.
Color saturation: Ink with high or low viscosity can cause uneven distribution of pigment particles, thereby affecting the color saturation of printed materials. Moderate viscosity helps to evenly disperse pigment particles in ink, making printed colors more vivid and full.
3. Printing speed and production efficiency
Printing speed: UV ink with appropriate viscosity can adapt to higher printing speeds, ensuring stable printing quality during rapid printing processes. Ink with high or low viscosity may limit printing speed and affect production efficiency.
Stability: Stable viscosity helps ink maintain consistent printing results over long periods of time, reducing quality issues caused by viscosity changes.
4. Curing effect and adhesion
Curing effect: The curing effect of UV ink is closely related to viscosity. Appropriate viscosity helps ink to solidify quickly and uniformly under ultraviolet irradiation, forming a strong ink film. Low viscosity may lead to incomplete ink curing, affecting the wear resistance and weather resistance of the ink film.
Adhesion: UV ink with moderate viscosity can better adhere to the substrate and form a firm ink film. Low viscosity may lead to insufficient adhesion between ink and substrate, resulting in ink loss or discoloration.
5. Static electricity and printing stability
Static electricity problem: During the printing process, the viscosity of ink may also affect the generation of static electricity. Although UV ink itself is not prone to static electricity, ink with high or low viscosity may increase the risk of static electricity generation in certain situations, affecting printing stability and quality.
In summary, the viscosity of UV ink has multiple impacts on printing quality. In the actual printing process, the viscosity of ink should be adjusted reasonably according to specific printing equipment, substrate, printing speed and other conditions to ensure the best printing effect and quality.