How can I ensure the best results when using water-based ink printing on plastic film
Date: Aug 12 2023 From: Star Color Views:
When using water-based ink printing on plastic film, there are several steps you can take to ensure the best results. Here are some guidelines to follow:
1.Select the right ink: Ensure that the water-based ink you choose is specifically formulated for printing on plastic films. Different inks are designed for different substrates, and using the appropriate ink will improve adhesion and color vibrancy.
2.Surface preparation: Properly prepare the plastic film surface before printing. Clean it thoroughly to remove any dirt, oils, or contaminants that may interfere with ink adhesion. Use a mild detergent or a specialized cleaning solution recommended for plastic films. Rinse and dry the film completely before printing.
3.Test compatibility: Before initiating a full production run, perform a small-scale test print on a sample piece of plastic film. This will help you determine the compatibility of the ink with the specific film material and identify any potential issues beforehand.
4.Ink viscosity: Maintain the proper viscosity of the ink for optimal printing. The viscosity affects ink flow and penetration into the film. Follow the manufacturer's recommendations for ink viscosity and use a viscosity cup or a viscometer to measure and adjust the ink consistency as needed.
5.Ink drying/curing: Ensure sufficient drying or curing time for the ink. Water-based inks typically require longer drying times compared to solvent-based inks. Use drying racks or a drying tunnel with controlled temperature and airflow to facilitate proper ink drying. If necessary, use infrared or UV curing methods, depending on the ink type and equipment availability.
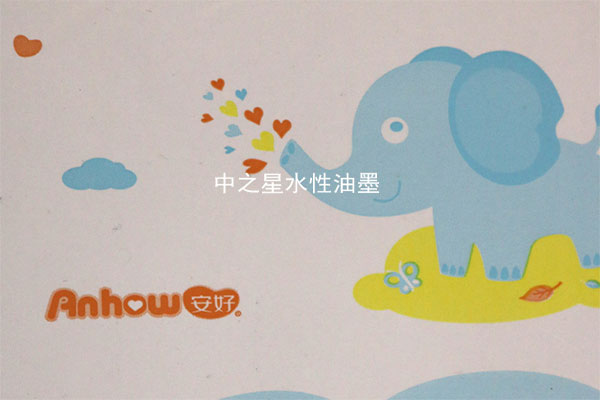
6.Adhesion promotion: Enhance ink adhesion by using adhesion promoters or primers designed for plastic films. These products can improve ink anchorage and prevent ink from rubbing off or scratching easily. Consult with ink and primer manufacturers to determine the most suitable products for your specific application.
7.Maintain stable printing conditions: Control the printing environment to ensure stable conditions throughout the printing process. Fluctuations in temperature and humidity can impact ink drying and adhesion. Ideally, maintain a controlled environment with stable temperature, humidity, and ventilation.
8.Proper handling and storage: After printing, handle the plastic film carefully to avoid scratching or damaging the printed surface. Allow sufficient curing or drying time before further processing or packaging. Properly store the printed films in a controlled environment to maintain ink integrity and prevent moisture absorption or contamination.
9.Quality control and testing: Implement a thorough quality control process to inspect the printed films for color accuracy, ink adhesion, and overall print quality. Regularly test samples to ensure the desired results are consistently achieved.
By following these guidelines and working closely with your ink supplier, you can increase the chances of achieving the best results when using water-based ink printing on plastic film.