Troubleshooting for UV Flexo Ink Printing
Date: Nov 05 2024 From: Star Color Views:
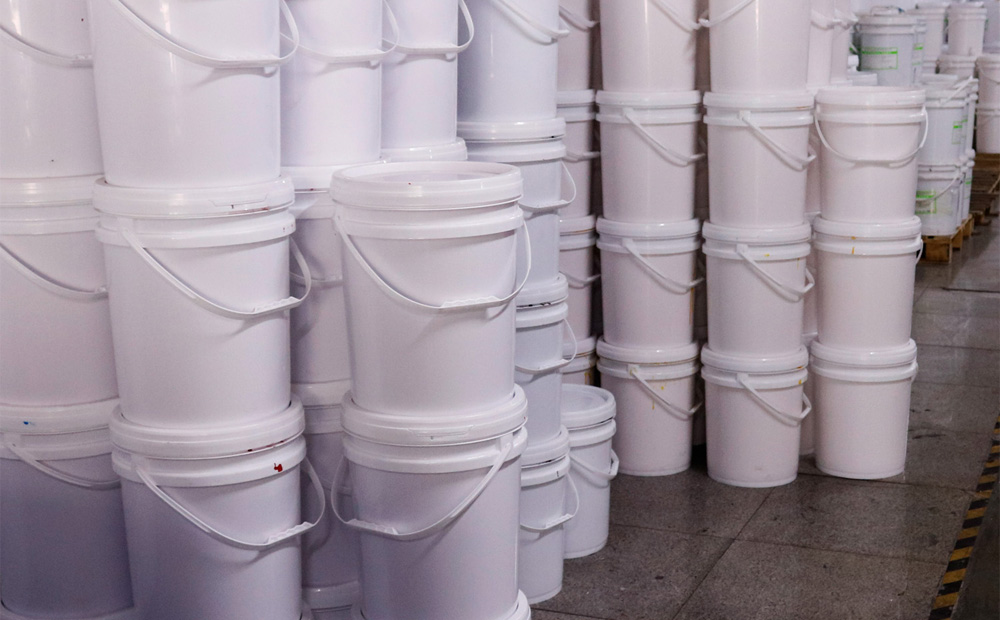
1. Poor Gloss and Luminance
Main Causes:
- The viscosity of the UV ink is too low, resulting in a thin coating.
- Excessive dilution with non-reactive solvents such as ethanol.
- Uneven coating of UV ink.
- Highly absorbent paper.
- Use of a fine anilox roller, insufficient ink supply.
Solutions:
- Appropriately increase the viscosity and coating thickness of the UV ink based on the paper type.
- Avoid excessive dilution with non-reactive solvents.
- Ensure even coating of the UV ink.
- Apply a primer layer for highly absorbent paper.
- Choose a suitable anilox roller to ensure adequate ink supply.
2. Ink Drying Too Quickly
Main Causes:
- Overpowered UV lamps.
- Excessively fast printing speed.
Solutions:
- Reduce the power of the UV lamps.
- Decrease the printing speed.
- Add appropriate additives to the UV ink to slow down the drying process and enhance color saturation.
3. Ink Stringing and Plate Fouling During Printing
Main Cause:
- Low viscosity of the UV ink.
Solution:
- Increase the viscosity of the UV ink by adding appropriate amounts of resin.
- Clean the printing plate thoroughly before printing to avoid residue affecting the ink viscosity.
4. Bubbles in the Ink During Printing
Main Cause:
- Excessively high surface tension of the UV ink.
Solution:
- Add appropriate amounts of defoamer to the UV ink to reduce its surface tension and prevent bubble formation.
- Clean the printing plate thoroughly before printing to avoid residue affecting the ink's surface tension.
5. Poor Adhesion and Easy Fading of Printed Products
Main Causes:
- Incomplete curing of the UV ink.
- Low surface tension of the substrate.
- Poor bonding between the ink and the substrate.
Solutions:
- Increase the power of the UV lamps or extend the curing time.
- Ensure that the surface tension of the substrate meets the requirements of the UV ink.
- Conduct strict degreasing and pretreatment inspections of the substrate to ensure it is free of oils, adhesives, dust, and other contaminants.
- Apply a reinforcing liquid to the printed surface or increase the amount of UV ink to improve adhesion.
- Choose a suitable UV ink that is compatible with the substrate.
6. Thickening and Gelation of the Ink
Main Causes:
- Prolonged storage of the UV ink.
- Failure to store the UV ink in complete darkness.
- High storage temperatures.
Solutions:
- Pay attention to the expiration date of the UV ink and store it in complete darkness.
- Store the ink at a temperature between 5°C and 25°C.
7. Ink Supply Failures
Main Causes:
- Incorrect installation of the ink cartridge.
- Clogged ink tubing.
- Empty or low ink levels in the cartridge.
- Print head malfunction.
- Ink supply system failure.
Solutions:
- Ensure the ink cartridge is installed correctly and is not expired or damaged.
- Clean the ink tubing. If you suspect clogging, use a dedicated cleaning tool or method.
- Check the ink level in the cartridge using the printer's control panel or related software and replace or refill as needed.
- Inspect the print head for signs of clogging or damage, and clean or replace it as recommended in the printer's manual.
- If the above steps do not resolve the issue, contact the printer manufacturer or technical support team for further assistance.
The above are the common problems and solutions that UV flexographic ink often encounters during printing. We hope it is helpful to you. Troubleshooting UV flexographic ink requires starting from multiple aspects, including the quality of the ink itself, adjustment of printing equipment, handling of printing materials, and control of the printing environment. You can also contact me to assist you in solving problems during the printing process