Common Issues with Gravure Ink: Troubleshooting and Solutions
Date: Jan 07 2025 From: Star Color Views:
Gravure printing, known for its high-quality reproduction and versatility, is a popular choice for packaging, publications, and other large-scale print applications. However, like all printing processes, gravure printing can come with its own set of challenges, particularly when it comes to ink performance. Gravure ink issues can lead to defects such as poor print quality, operational delays, and increased costs.
1. Ink Smudging or Blurring
Cause:
Smudging or blurring occurs when the ink does not dry properly or adheres too loosely to the substrate. This is a common issue in high-speed gravure printing, where fast drying and quick handling are essential. Several factors may contribute to smudging, including:
- Slow drying time: Inadequate drying processes or improper ink formulations.
- Ink viscosity: If the ink is too thin or too thick, it may not dry correctly or could smear when touched.
- Environmental conditions: High humidity or inadequate air circulation can slow the drying process.
Solution:
- Optimize drying speed: Ensure proper drying mechanisms, such as hot air or infrared drying, are in place to speed up evaporation.
- Adjust ink viscosity: Use a viscosity modifier to achieve the right thickness, ensuring the ink adheres well but dries quickly.
- Improve environmental controls: Maintain a stable humidity and temperature in the printing area to enhance drying efficiency.
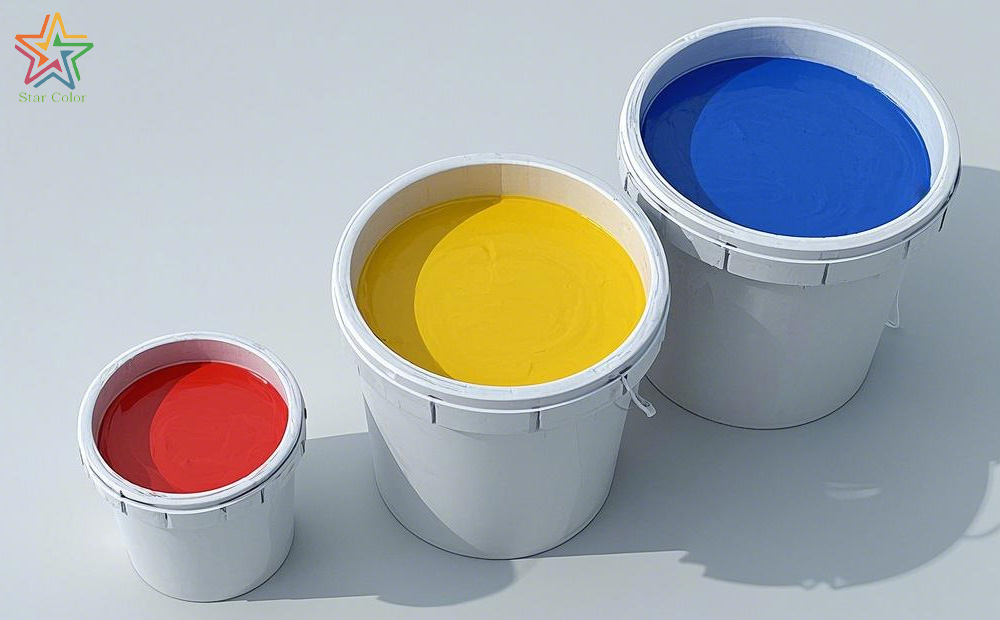
2. Poor Adhesion to Substrate
Cause:
Poor adhesion can cause the ink to peel, scratch, or fade away from the substrate. This is especially problematic for packaging materials that need to endure handling and transportation. Factors contributing to poor adhesion include:
- Improper substrate preparation: Insufficient cleaning or surface treatment of the substrate can affect ink adhesion.
- Incompatible ink formulation: The ink may not be designed to adhere to the specific material or coating of the substrate.
- Low-quality ink: Low-quality or improperly mixed inks may fail to bond effectively with the surface.
Solution:
- Surface treatment: Ensure proper surface treatment of substrates, such as corona treatment or flame treatment, to enhance ink adhesion.
- Use specialized inks: Select ink formulations specifically designed for the material being printed on (e.g., plastic films, foil, or paper).
- Increase ink curing time: Allow adequate drying or curing time to improve the bond between the ink and the substrate.
3. Uneven Ink Coverage
Cause:
Uneven ink coverage results in inconsistent print quality, with some areas being darker or lighter than others. This is often caused by:
- Inconsistent ink viscosity: If the ink’s viscosity is not stable, it may spread unevenly across the substrate.
- Cylinder or anilox roller issues: A worn or improperly cleaned anilox roller can transfer inconsistent amounts of ink to the printing cylinder.
- Inaccurate engraving depth: If the engraving depth of the cylinder is too shallow or too deep, it may not transfer the ink evenly.
Solution:
- Monitor ink viscosity: Regularly check and adjust ink viscosity for consistency, ensuring it remains within the optimal range for the job.
- Clean and maintain rollers: Regularly clean anilox rollers and cylinders to ensure even ink transfer. Consider using anilox rollers with appropriate cell volumes for the specific ink type and substrate.
- Inspect cylinder engraving: Check cylinder engraving for any wear or damage that may be causing uneven ink deposition.
4. Poor Color Consistency
Cause:
In gravure printing, maintaining color consistency across different print runs can be challenging. Inconsistent colors can be caused by:
- Ink batch variation: Differences between ink batches can lead to slight color mismatches.
- Improper mixing or formulation: Inaccurate ink mixing or unbalanced pigment levels can result in color inconsistency.
- Environmental changes: Temperature or humidity fluctuations can alter ink behavior and affect color reproduction.
Solution:
- Standardize ink mixing: Use automated ink mixing systems to ensure consistent color formulation across batches.
- Control environmental conditions: Keep the printing environment’s temperature and humidity stable to avoid fluctuations that may affect ink consistency.
- Monitor color quality: Use spectrophotometers or color management systems to continuously monitor and adjust ink color during production.
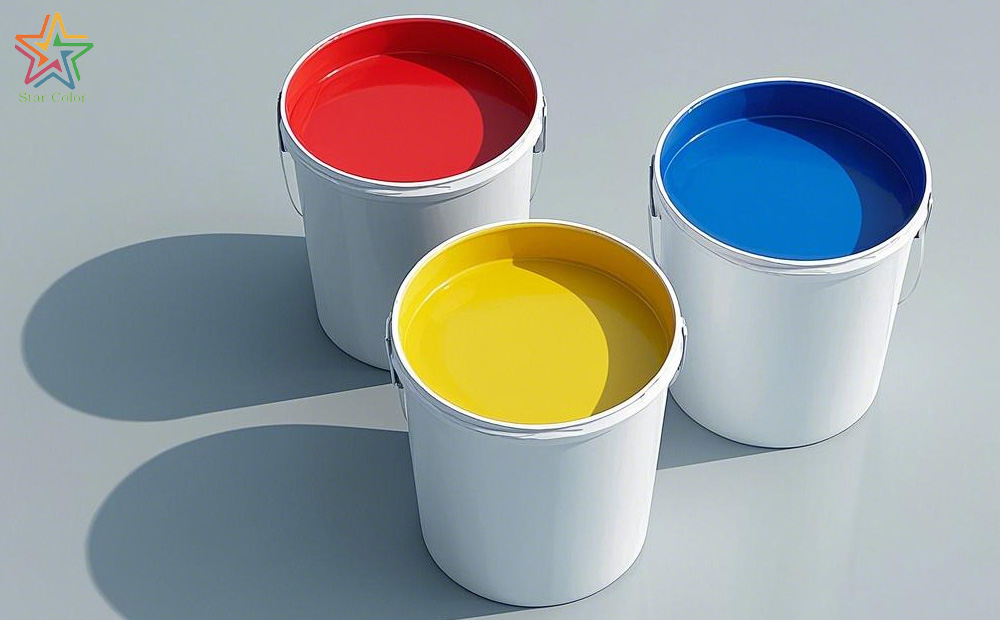
Gravure ink issues can have a significant impact on print quality, operational efficiency, and costs. By understanding the common problems that arise with gravure ink—such as smudging, poor adhesion, ink misting, uneven coverage, and color inconsistency—printers can take proactive steps to troubleshoot and resolve these issues.