How to improve the glossiness of water-based ink?
Date: Jan 22 2025 From: Star Color Views:
Many people say that the glossiness of
water-based ink is not as good as oil-based ink, so they refuse to use water-based ink to ensure the quality of printed materials. Indeed, the glossiness of water-based ink is not as good as oil-based ink, but there is not a big gap. Huizhou Zhongxing has conducted in-depth research and improvement on the glossiness of water-based ink, which has greatly improved its glossiness. In some non absorbent materials, it is even not much worse than oil-based ink.
Let's take a look at a case study together,There is a packaging printing company (hereinafter referred to as Company A) that mainly engages in food packaging printing business. Its products have extremely high requirements for glossiness and vivid colors. In previous production, when using traditional water-based ink formulas, the glossiness of printed products could only reach about 60GU, which could not meet the strict requirements of high-end customers for product appearance. In order to improve this situation, many water-based inks were tested, and after screening and comparison, it was finally decided to collaborate with Huizhou Zhongzhixing to develop a high gloss water-based ink.
Firstly, in terms of ink formula optimization, Zhongzhixing has re screened the resin and pigment. After multiple experimental comparisons, a high-performance acrylic resin was selected, combined with imported pigments with smaller particle size and better dispersibility. At the same time, the ratio of resin to pigment was adjusted to 5:1, effectively improving the glossiness of the ink. In addition, an appropriate amount of wax lotion and silicone brightener were added to further enhance the gloss effect of the ink.
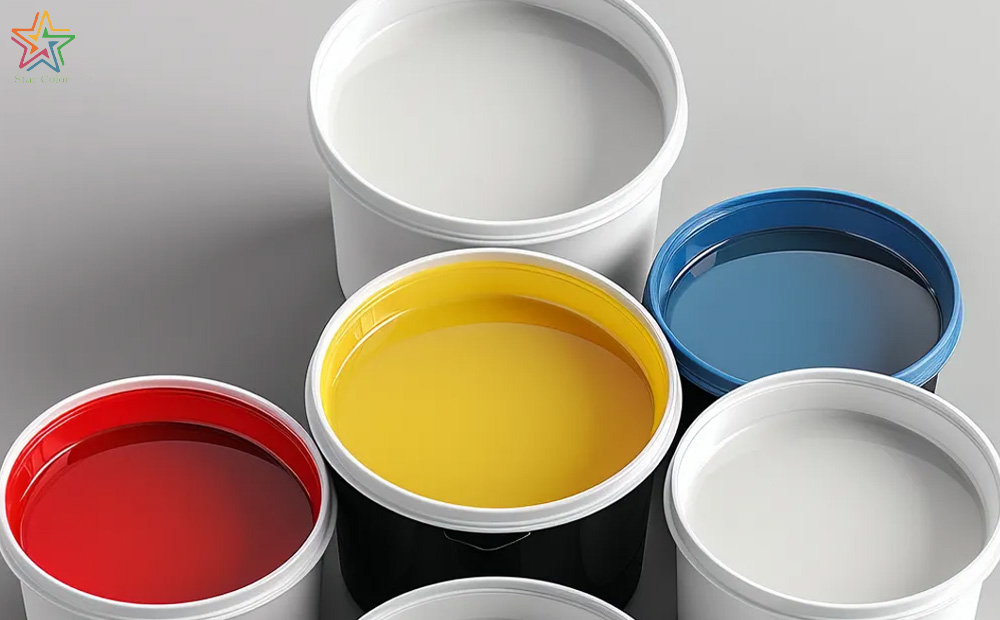
In terms of improving printing technology, Company A has invested funds to upgrade its printing equipment, installing high-precision ink volume control systems and advanced drying devices. By precisely adjusting parameters such as printing pressure, speed, temperature, and time, it is ensured that the printing pressure is stable at around 3MPa, the printing speed is controlled at 150 meters per minute, and the drying temperature is set at 65 ℃. This parameter setting enables ink to be evenly transferred onto the printing substrate and form a smooth and flat ink film after drying.
For printing substrates, Company A has carried out special coating treatment on the paper, applying a thin layer of gloss enhancing coating on the surface of the paper, effectively filling the pores on the surface of the paper and increasing the smoothness of the surface. In terms of printing environment control, an automatic temperature and humidity adjustment system has been installed to stabilize the temperature in the printing workshop at 22-26 ℃ and maintain the humidity at around 50%. At the same time, the ventilation and air exchange in the workshop have been strengthened, and air purification equipment has been installed to ensure good and clean air circulation.
After a series of improvement measures, the glossiness of Company A's printed materials has been significantly improved, reaching over 85GU. This achievement not only meets the needs of high-end customers, but also wins more market share for the company. When the product is displayed on the shelf, it attracts the attention of many consumers with its high glossiness and bright colors, effectively enhancing the competitiveness of the product.
Data comparison displayBy comparing the data of A company's printed products before and after improvement, we can more intuitively see the improvement effect of glossiness and printed product quality. In terms of glossiness, the average glossiness before the improvement was 60GU, but after the improvement it reached over 85GU, an increase of over 40%. From the perspective of the vividness of printed materials, the color saturation before improvement was relatively low, and the color presentation was relatively dull; After improvement, due to the increase in glossiness and optimization of ink formula and printing process, the color saturation is significantly enhanced, and the colors are more vivid and lively.
In terms of surface flatness of printed materials, there are some minor flaws on the surface of the printed materials before improvement, such as flow marks, orange peel, etc., which affect the overall aesthetics; After improvement, by optimizing the printing process and processing the substrate, the surface of the printed product becomes smooth and even, with almost no obvious defects visible. In actual sales, products printed with improved water-based ink have received good market feedback, and consumer satisfaction with product packaging has significantly increased. According to relevant data, the sales of this product increased by 30% within six months after improvement, fully demonstrating the positive impact of improving the glossiness of water-based ink on product market performance.
For more information on water-based inks, please contact eva@starcolor-ink.com .