Can screen printing ink and offset printing ink be shared?
Date: Feb 01 2025 From: Star Color Views:
In the printing industry, screen printing ink and offset printing ink are two common types of ink. Some people notice that their viscosities are relatively close, and they may wonder: can these two inks be used together? Today, we will conduct a comprehensive comparison between screen printing ink and offset printing ink.
Different working principles
The working principle of screen printing inkScreen printing is the process of transferring ink onto the substrate through the mesh holes of the screen plate by squeezing with a scraper. Due to the fact that the mesh holes in the graphic and textual parts of the screen plate allow ink to pass through, while the blank mesh holes are blocked and ink cannot pass through, it is possible to form graphic and textual images on the substrate that are identical to the original manuscript. In this process, high viscosity screen printing ink is forced to pass through the mesh under the force of the scraper, which requires the ink to have good thixotropy, that is, the viscosity decreases when subjected to external force, making it easy to flow, and can quickly recover high viscosity after the external force disappears, preventing the ink from flowing freely on the screen.
The working principle of offset printing inkOffset printing utilizes the principle of oil water incompatibility. The graphic and textual parts on the printing plate are hydrophilic and hydrophobic, while the blank parts are hydrophilic and hydrophobic. First, supply water to the printing plate to form a water film on the blank area, and then supply ink to absorb the ink on the graphic and text parts. Then, the ink is first transferred to the rubber blanket, and finally transferred to the substrate through the rubber blanket. In the process of offset printing, ink needs to be stably transferred between the ink rollers, from the ink hopper to the printing plate, and then to the rubber blanket and substrate. High viscosity offset ink can ensure that it will not excessively diffuse during the transfer process, maintain accurate ink transfer, and ensure the clarity of the printed pattern.
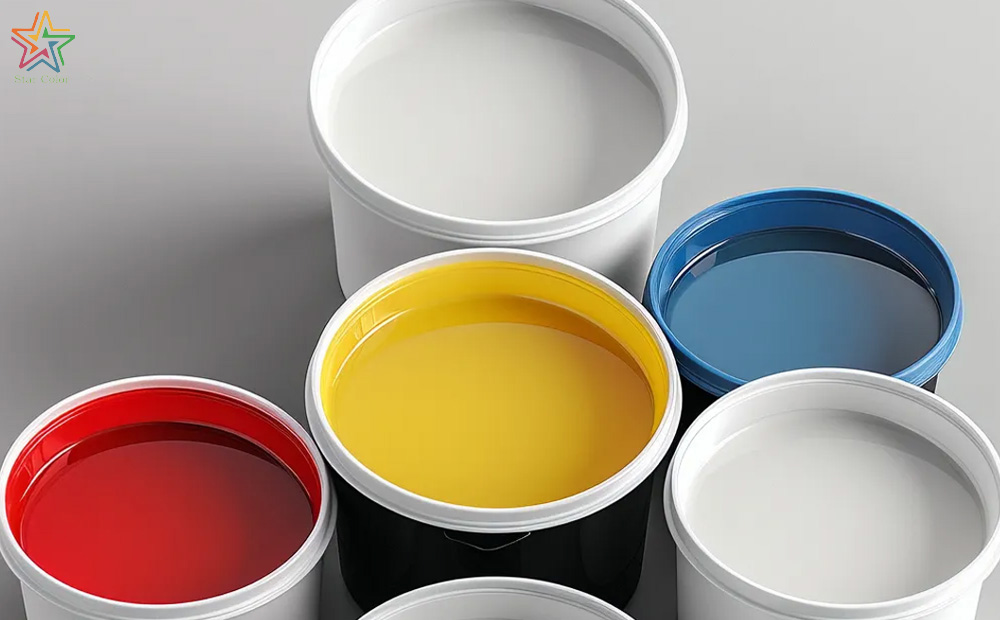
Significant differences in ink characteristics
Different drying methodsThere are various drying methods for silk screen ink, including natural drying, hot air drying, ultraviolet drying, etc. During natural drying, the solvent in the ink slowly evaporates, causing the ink to solidify; Hot air drying accelerates solvent evaporation by heating; UV drying is the process of using ultraviolet light to trigger a reaction of the photoinitiator in the ink, resulting in rapid curing of the ink.
Offset printing ink mainly relies on oxidation film and permeation drying. After printing, dry vegetable oil and other components in the ink undergo oxidative polymerization reaction with oxygen in the air, forming a tough ink film. At the same time, some ink will penetrate into the interior of the paper, quickly fixing the ink film on the surface of the paper.
The ingredients are different
Screen printing ink has complex components, including resin, pigment, solvent, additives, etc. Different types of screen printing ink have significant differences in their composition ratios. For example, silk screen printing ink used for fabric printing may add some special additives to enhance the adhesion between the ink and fabric fibers; The silk screen ink used for plastic printing will choose resins and solvents that are compatible with plastic materials.
The main components of offset printing ink are also resin, pigment, solvent, and additives. However, in order to meet the ink balance requirements of offset printing, the resin and solvent in offset printing ink need to have special chemical structures to ensure that the ink will not emulsify or have other adverse effects when in contact with water, and to ensure the stability of printing quality.
Each printing effect has its own advantages
Ink layer thicknessScreen printing can achieve thick ink layer printing, with ink layer thickness generally ranging from 10-30 μ m or even thicker. This gives silk screen printing a significant advantage in printing patterns with three-dimensional and textured requirements, such as printing Braille, logos on circuit boards, etc.
The ink layer of offset printing is relatively thin, usually around 1-3 μ m. A thinner ink layer can ensure the delicacy and clarity of printed patterns, suitable for printing high-precision content such as text, images, etc., such as books, magazines, etc.
Color expression
The color saturation of silk screen ink is high, which can present bright and rich colors. Due to the thick ink layer and relatively high pigment concentration in silk screen printing, it stands out in color expression, especially suitable for printing patterns that require strong visual impact.
Offset printing ink expresses the depth and hierarchy of colors through the size and density of the dots, with natural and delicate color transitions that can achieve high-precision color reproduction. It has advantages in printing color images, brochures, and other aspects.
Can it be shared?
Although the viscosity of screen printing ink and offset printing ink is relatively close,
considering the differences in all aspects mentioned above, the two cannot be shared. From the perspective of working principle, screen printing relies on scraper squeezing through the mesh, while offset printing relies on oil-water incompatibility and ink roller transmission. Different working methods determine different requirements for ink fluidity, thixotropy, and other properties. In terms of ink characteristics, the differences in drying methods and composition also make it impossible for them to work properly in each other's printing environment.
For example, if the drying method of silk screen ink is used for offset printing, it may cause the drying speed to be too fast or too slow, affecting printing efficiency and quality; If the components of offset printing ink are used for screen printing, they may not be well compatible with screen printing plates and substrates. In terms of printing effect, the two pursue different ink layer thickness and color expression, and sharing ink cannot achieve their respective ideal printing effects.