Comparison of Migration Levels Between UV Inks and Water-based Inks
Date: Jul 17 2025 From: Star Color Views:
Currently, UV inks and water-based inks are two mainstream ink systems in packaging printing. What are the differences between them in terms of migration performance? Which type of ink is more suitable for migration-sensitive packaging? This article provides a comprehensive analysis for you.
1. What is Ink Migration?
Ink migration refers to the transfer of low-molecular substances in printing inks into food or pharmaceuticals through various pathways. Common migration methods include:- Direct migration: The printing layer is in direct contact with the product.
- Set-off migration: During the rolling or stacking process, the ink surface comes into contact with the food contact layer.
- Gas-phase migration: Volatile components in the ink evaporate and deposit on the product.
- Penetration migration: Ink components penetrate through the packaging material itself to the contents.
2. Migration Characteristics of UV Inks
UV inks achieve instant curing through ultraviolet-induced polymerization of photoinitiators and acrylate monomers.Main migration risks:
- Unreacted monomers or oligomers: If curing is insufficient, residual reactive substances may migrate.
- Residual photoinitiators: Most photoinitiators have small molecular weights and are prone to migration.
- Web set-off migration: The printed ink surface may come into contact with the inner packaging surface.
Advantages:
- Rapid curing, suitable for high-speed printing.
- Excellent film-forming properties, with abrasion resistance and solvent resistance.
Migration level performance:
Unless UV inks specifically designed for low migration are used, the migration risk is relatively high. Compliant low-migration UV inks will adopt:
- High-molecular-weight photoinitiators;
- High-efficiency curing systems;
- Raw materials that meet U.S. FDA, EU food contact regulations, etc.
3. Migration Characteristics of Water-based Inks
Water-based inks mainly consist of water, pigments, acrylic emulsions, and a small amount of additives.Natural low-migration advantages:
- No photoinitiators or acrylate monomers;
- Use of high-molecular-weight emulsion resins;
- Extremely low volatile components, almost no organic solvents.
Potential risks:
- Individual additives (such as defoamers, preservatives) may still have migration risks if food-grade raw materials are not selected.
Migration level performance:
Water-based inks usually have very low migration levels, making them particularly suitable for paper substrates and indirect food contact packaging.
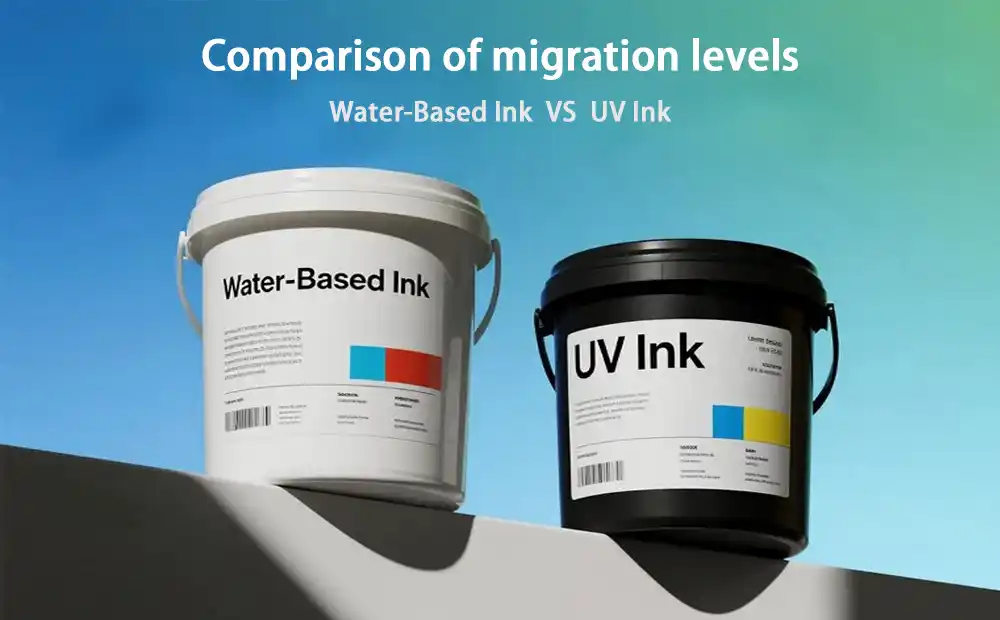
4. Comparison of Migration Performance Between UV Inks and Water-based Inks
Item | UV Inks | Water-based Inks |
---|---|---|
Curing method | UV curing (photoinitiated polymerization) | Heat drying (physical drying + partial film formation) |
Main migration risks | Photoinitiators, unpolymerized monomers | Residual additives (very few) |
Volatile components | Low, but photoinitiators may migrate | Mainly water, extremely low VOC |
Typical migration performance | Medium to high (requires specialized formulation) | Extremely low (natural advantage) |
Suitable for food packaging | Requires low-migration formulation, used with functional barrier layers | Suitable for paper packaging or indirect contact applications |
Compliance difficulty | High, requires migration testing + documentation support | Relatively low, but still needs to comply with regulations |
In summary:
- Water-based inks, due to their natural characteristics, have low migration levels and are usually easier to meet EU and FDA standards.
- UV inks can also meet low-migration requirements through strict control of raw material selection and systematic migration testing.
5. StarColor's Solutions
At StarColor, we offer:Low-migration UV inks:
- Adopt high-molecular-weight photoinitiators;
- All formula raw materials meet U.S. FDA testing, with test reports available.
- High curing efficiency, low residues;
- Can provide third-party migration test reports and compliance statements.
Low-VOC water-based inks:
- Use food-grade additives;
- Strong film formation, excellent water resistance;
- Suitable for cardboard, kraft paper, labels, paper bags, and other recyclable packaging.
Each of our products is designed to meet major international regulations, including:
- EU 1935/2004
- U.S. FDA 21 CFR
Conclusion
In the printing and packaging industry, controlling migration is not only about regulatory compliance but also a commitment to consumer health. Water-based inks, with their naturally low migration characteristics, are the first choice for food packaging, while UV inks can also meet low-migration requirements through precise formulation control and strict testing.At StarColor, we are committed to providing customers with high-performance and compliant safe water-based and UV printing solutions to help you gain brand recognition and trust in the global market.