What are some strategies for achieving consistent color in water-based ink production
Date: Aug 07 2023 From: Star Color Views:
1.Precise formulation: Develop and maintain accurate ink formulations using standardized recipes and precise measurement techniques. Carefully control the concentration and quality of colorants, binders, and other additives to ensure consistent color reproduction.
2.Quality control protocols: Implement stringent quality control protocols throughout the production process. Regularly test and analyze ink samples to verify color consistency using color measurement instruments, such as spectrophotometers or colorimeters.
3.Proper dispersion of pigments: Ensure thorough and uniform dispersion of pigments during the ink manufacturing process. Use appropriate dispersing agents and milling techniques to achieve optimal pigment distribution and prevent color variations.
4.Standardized mixing procedures: Follow standardized mixing procedures to ensure consistent ink blending. Adhere to specific mixing times, speeds, and order of ingredient addition to achieve uniform color throughout the ink batch.
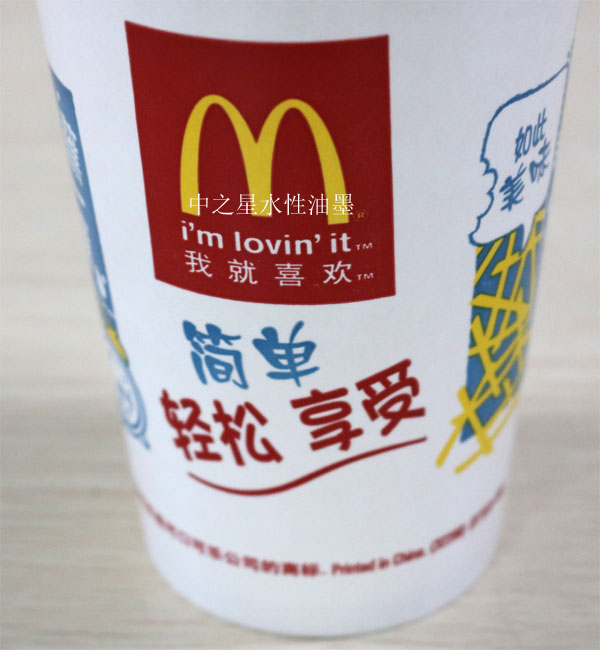
5.Color matching and correction: Establish color matching procedures to compare the produced ink's color with a desired target. If variations are detected, employ corrective measures such as adjusting the pigment concentration, adding colorants, or modifying the formulation to achieve the desired color consistency.
6.Consistent raw material sourcing: Maintain consistency in the sourcing of raw materials, such as pigments and additives, from reliable suppliers. This helps ensure batch-to-batch color consistency and minimizes variations caused by material quality differences.
7.Standardized printing conditions: If the ink is intended for specific printing processes, establish standardized printing conditions, including substrate type, printing equipment settings, and curing/drying parameters. This helps maintain consistency between the produced ink and the final printed output.