How to control the viscosity of flexographic water-based ink?
Date: Sep 22 2024 From: Star Color Views:
The viscosity control of
water-based ink is a key step in ensuring stable and efficient printing quality during flexographic printing. The following will elaborate on how to accurately control the viscosity of water-based ink from multiple aspects.
Standard range of viscosity for water-based ink
The viscosity of water-based ink usually varies depending on printing requirements and ink type, but generally follows a certain standard range. For example, the viscosity of ordinary water-based ink is generally controlled between 50-65 seconds when measured using a No. 4 cup at 25 ℃; The viscosity of high-end water-based ink is relatively low, possibly between 25-35 seconds. For example, Zhongzhixing's flexographic water-based ink adopts a high concentration, low viscosity formula, with viscosity basically maintained between 22-32. These standard ranges help printing personnel to preliminarily judge the applicability of the ink.
Factors affecting the viscosity of water-based ink and quantitative analysis
1. Ink composition
Pigment content: The size and distribution of pigment particles directly affect the fluidity of ink. The higher the pigment content, the higher the viscosity of the ink. Some specific colors of ink may require higher pigment content to achieve the desired color saturation, but this will also correspondingly increase the viscosity of the ink.
Resin type: Different types of resins also have a significant impact on the viscosity of ink. High molecular weight resins often give ink higher viscosity.
2. Environmental conditions
Temperature: Temperature is one of the most direct factors affecting ink viscosity. Generally speaking, for every 10 ℃ increase in temperature, the viscosity of the ink will decrease by about half. Therefore, in high temperature environments during summer, it may be necessary to maintain appropriate viscosity by reducing ink temperature or adding thickeners.
Humidity: Humidity also affects the viscosity of water-based ink. Prolonged high humidity environments may cause the ink to absorb moisture from the air, leading to changes in viscosity. In environments with low humidity, the moisture in water-based ink may evaporate and cause surface peeling.
3. Printing speed and pressure
Printing speed: Faster printing speed requires ink to have lower viscosity to ensure smooth transfer. On the contrary, during low-speed printing, the ink viscosity can be appropriately increased to achieve better printing results.
Printing pressure: Appropriate printing pressure helps to evenly transfer ink, but excessive pressure may lead to excessive ink penetration, affecting the stability of viscosity.
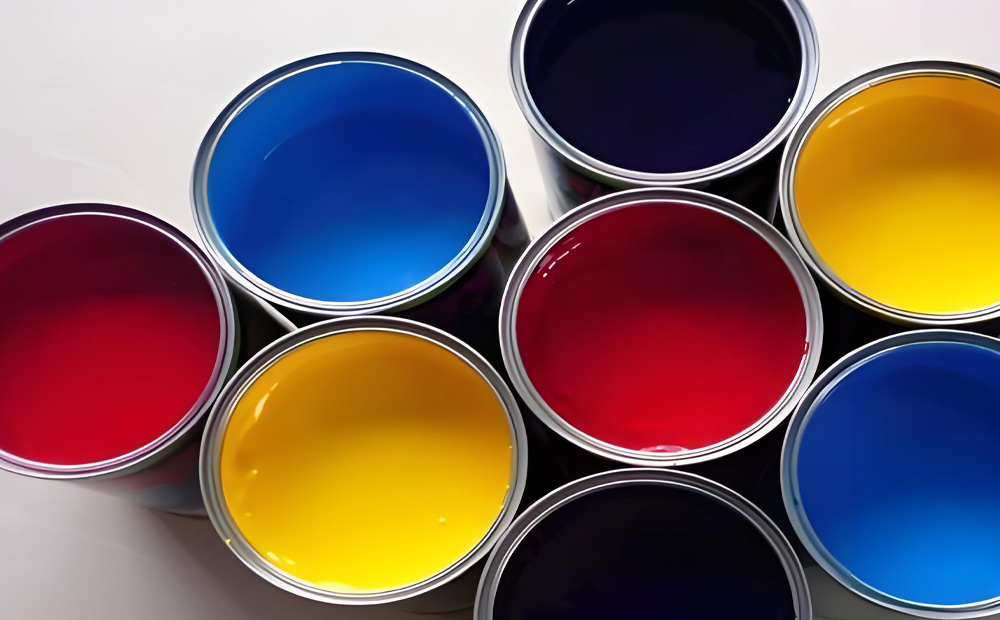
Method for precise control of water-based ink viscosity
1. Use professional measuring instrumentsRotational viscometer: Determine the viscosity value of ink by measuring its rotational resistance under specific conditions. This instrument has high precision and repeatability, making it the preferred tool for controlling ink viscosity.
Chaen cup: Another commonly used viscosity measurement tool, suitable for rapid on-site testing. Determine the viscosity of the ink by observing the time it flows out of the cup.
2. Accurately mix inkDiluents and thickeners: Accurately add an appropriate amount of diluent or thickener according to the actual viscosity value of the ink and printing requirements for adjustment. Generally speaking, the amount of diluent added should be controlled within 5% of the total ink volume to avoid excessive impact on ink performance.
Mixing evenly: During the mixing process, it is important to ensure that the ink is thoroughly mixed to avoid uneven concentration in certain areas.
3. Control environmental conditionsConstant temperature and humidity: Install constant temperature and humidity equipment in the printing workshop to control the temperature and humidity within a certain range (such as 20-25 ℃, 50% -60% humidity), in order to reduce the influence of environmental factors on ink viscosity.
4. Monitor the printing processRegular inspection: Regularly check the viscosity value and usage of ink during the printing process to ensure that it fluctuates within the standard range.
Timely adjustment: Once the ink viscosity deviates from the standard range or the printing effect is poor, the machine should be stopped immediately to check and adjust the ink formula or process parameters.
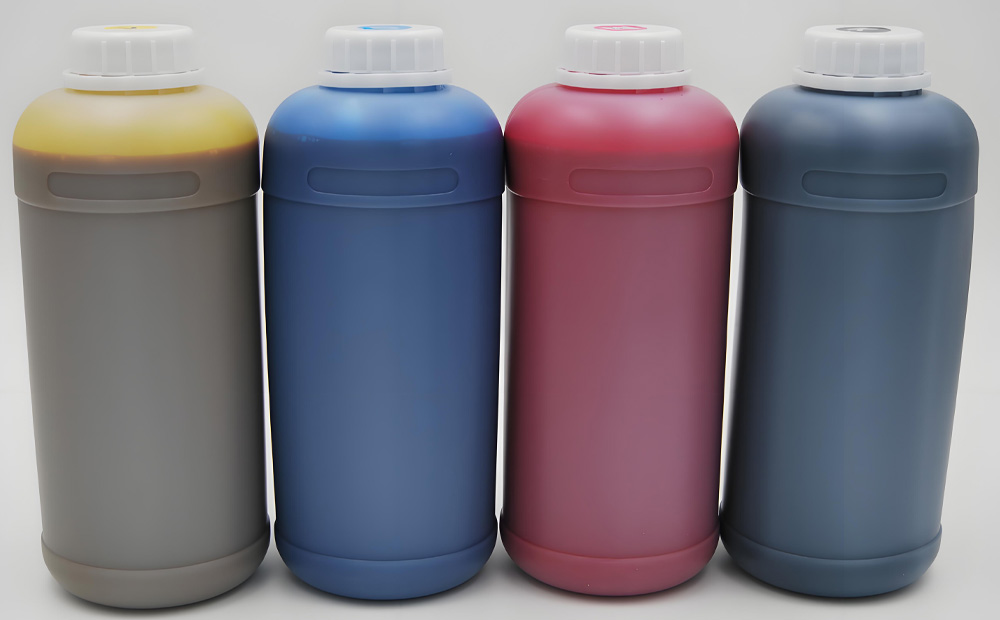
Accurate control of water-based ink viscosity can be achieved through scientific methods and precise control measures. This not only helps improve the quality and stability of printed materials, but also reduces production costs and improves production efficiency.
The
water-based ink produced by Zhongzhixing Color has bright colors, high color intensity, and good color stability. This is due to its use of high concentration, low viscosity formula design, which enables printed materials to maintain long-term brightness and consistency in color. Whether used in food packaging, paper printing, or other fields, we can ensure that the color effect of printed materials meets customer requirements.