How to Select the Right UV Flexo Ink for High-Speed Printing
Date: Dec 04 2024 From: Star Color Views:
High-speed printing demands inks that can keep up with the pace while delivering exceptional quality and performance. In UV flexographic printing, the choice of ink plays a critical role in ensuring smooth operations, vibrant prints, and cost efficiency. Selecting the right UV flexo ink requires a careful evaluation of factors ranging from press speed to substrate compatibility.
Key Considerations for Selecting UV Flexo Ink
1. Compatibility with High-Speed Printing
UV flexo inks for high-speed printing must exhibit excellent flow properties to ensure consistent application at elevated press speeds. Look for inks with:
- Fast Curing: Rapid polymerization under UV light to prevent smudging and ensure immediate drying.
- Low Viscosity: To enable smooth transfer onto the substrate without compromising coverage.
2. Substrate Compatibility
The choice of ink should match the substrate being printed on. Common substrates include:
- Paper and Cardboard: Requires inks with strong adhesion and good surface penetration.
- Plastic Films: Needs inks with excellent flexibility and resistance to cracking or peeling.
- Foils and Laminates: Demands specialized formulations to maintain adhesion on non-porous surfaces.
Ensure that the ink is designed for the specific material to achieve optimal adhesion and durability.
3. Print Quality Requirements
High-speed printing does not mean sacrificing quality. UV flexo inks should deliver:
- Vivid Colors: High pigment concentration for vibrant, consistent hues.
- Sharp Details: Fine particle sizes for crisp, clear text and images.
- Scratch and Abrasion Resistance: Durability to withstand handling and storage.
Inks with enhanced opacity and gloss levels can further elevate the visual appeal of the printed product.
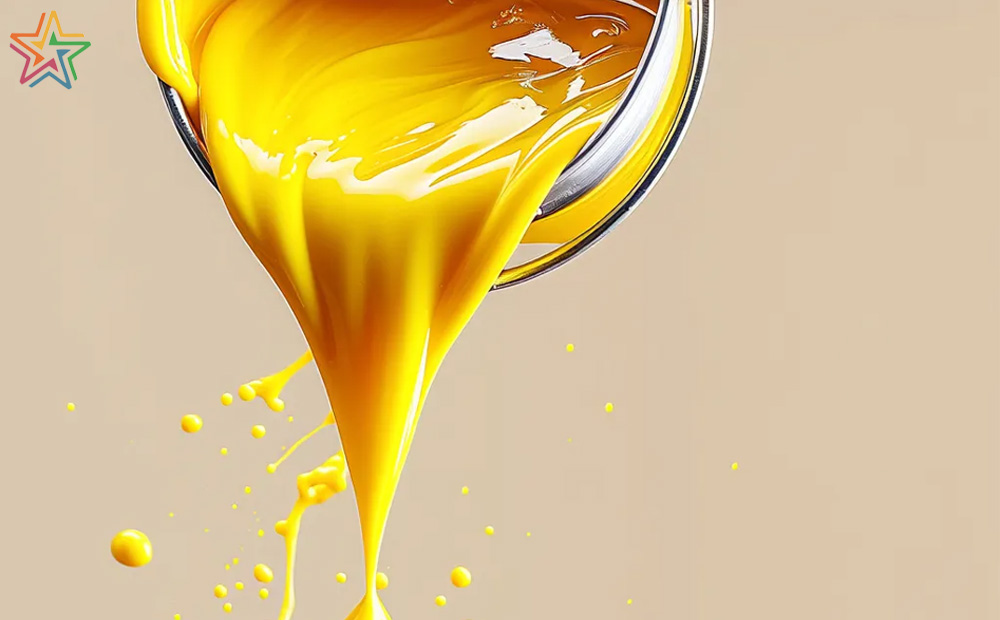
4. Ink Performance under Pressure
At high speeds, equipment operates under intense pressure and heat. UV flexo inks should have:
- Stable Viscosity: Consistency across varying temperatures and press conditions.
- Low Foaming Properties: To prevent defects during printing.
- Chemical Resistance: Especially for packaging that may encounter oils, solvents, or other substances.
5. Regulatory Compliance
For food packaging or other sensitive applications, ensure the ink complies with regulations such as:
- FDA Standards: For materials that may come into contact with food.
- REACH and RoHS Compliance: For environmental and health safety.
- Low Migration Properties: Prevents chemical migration into food or beverages.
6. Ease of Operation
Choose inks that minimize setup time and operational challenges. Key features include:
- Broad Cure Window: Ensures consistent curing under varying UV lamp intensities.
- Ink Stability: Long shelf life and minimal maintenance needs.
- Easy Cleanup: Reduces downtime and improves operational efficiency.
7. Cost Efficiency
While the upfront cost of ink is important, consider the overall value:
- Higher Yields: Inks with strong pigmentation may require less volume per print job.
- Reduced Downtime: Stable inks minimize interruptions due to defects or equipment issues.
- Energy Savings: Inks that cure efficiently can reduce UV lamp power consumption.
Partnering with the Right Ink Supplier
A reliable supplier is critical to ensuring success with UV flexo inks. Look for manufacturers that offer:
- Comprehensive Product Portfolios: Covering a wide range of substrates and applications.
- Technical Expertise: To provide guidance on ink selection and troubleshooting.
- Customization Options: Tailored formulations to meet specific printing needs.
- Proven Track Record: Positive reviews and case studies from high-speed printing applications.
Selecting the right UV flexo ink for high-speed printing involves balancing technical performance, substrate compatibility, and cost efficiency. By carefully evaluating your production requirements and working closely with a trusted ink supplier, you can achieve outstanding print quality while maximizing operational efficiency.