Can Water-Based Flexo Ink Replace Solvent-Based Ink in Flexible Packaging?
Date: Jul 21 2025 From: Star Color Views:
I. Strong Driving Force of Environmental Protection Regulations
In recent years, environmental protection regulations have become a key driving force for the rapid development of water-based inks, and their influence has penetrated into all aspects of the industry.The EU's REACH regulation not only strictly restricts VOC emissions but also clearly stipulates the use of various toxic substances that may be contained in inks. The implementation of this regulation has forced packaging and printing enterprises to conduct strict screening when choosing inks. Those solvent-based inks that do not meet the requirements are gradually eliminated from the market, greatly accelerating the market share of water-based inks.
China's "Emission Standard for Volatile Organic Compounds" (GB 37824) directly sets limit standards for the solvent content in inks. After the implementation of this standard, many printing enterprises have to invest a lot of money in transforming production equipment or replacing ink types to meet the emission requirements. This has, to a certain extent, accelerated the transformation of the industry towards environmentally friendly inks.
In addition to government regulatory requirements, some well-known food manufacturers and other brand owners have also begun to actively specify the use of low-VOC printing materials. In order to maintain their brand image and meet consumer needs, brand owners have successively added environmental protection indicators to the supply chain, which has further promoted the application of water-based inks in the field of flexible packaging printing.
Against this backdrop, water-based inks, which contain no or only extremely low levels of VOCs, naturally have policy advantages and have become an important choice for industrial transformation.
II. Technological Innovation of Water-based Flexographic Inks
Early water-based inks dried slowly, which affected printing efficiency. On non-absorbent films such as PET and BOPP, their adhesion was poor, making them difficult to be used for pre-lamination printing. Moreover, their water resistance and wear resistance were far inferior to solvent-based inks, which limited their application range.Nowadays, with the continuous advancement of technology, water-based flexographic inks have made significant improvements in many aspects:
The application of high-performance acrylic resins and self-crosslinking emulsions has effectively enhanced the adhesion and water resistance of water-based inks. Acrylic resins have good film-forming properties and adhesion, while self-crosslinking emulsions can form a cross-linked structure during the film-forming process, improving the compactness and water resistance of the ink film, making water-based inks perform better on various film materials.
The combination of fast-drying additive systems and hot air systems has greatly improved the drying speed of water-based inks. Fast-drying additives can reduce the surface tension of the ink and promote the evaporation of water, while the hot air system provides sufficient heat and air flow for water evaporation, accelerating the drying process.
The matching of special flexographic plates and anilox rollers can precisely control the ink transfer amount and ensure printing suitability. Different printing substrates and printing requirements require different ink transfer amounts. Special plates and anilox rollers can be adjusted according to actual needs to ensure that the ink can be evenly and stably transferred to the substrate, improving printing quality.
The application of online corona treatment and priming technology has increased the surface tension of the film, thereby enhancing the adhesion of water-based inks. Corona treatment can make the film surface generate polar groups and increase surface energy, while priming can form a uniform coating on the film surface, improving the bonding performance between the ink and the film.
Through these technical optimizations, water-based ink manufacturers such as StarColor have achieved stable printing on common flexible packaging substrates such as BOPP, PET, and PE, laying a solid technical foundation for the wide application of water-based inks.
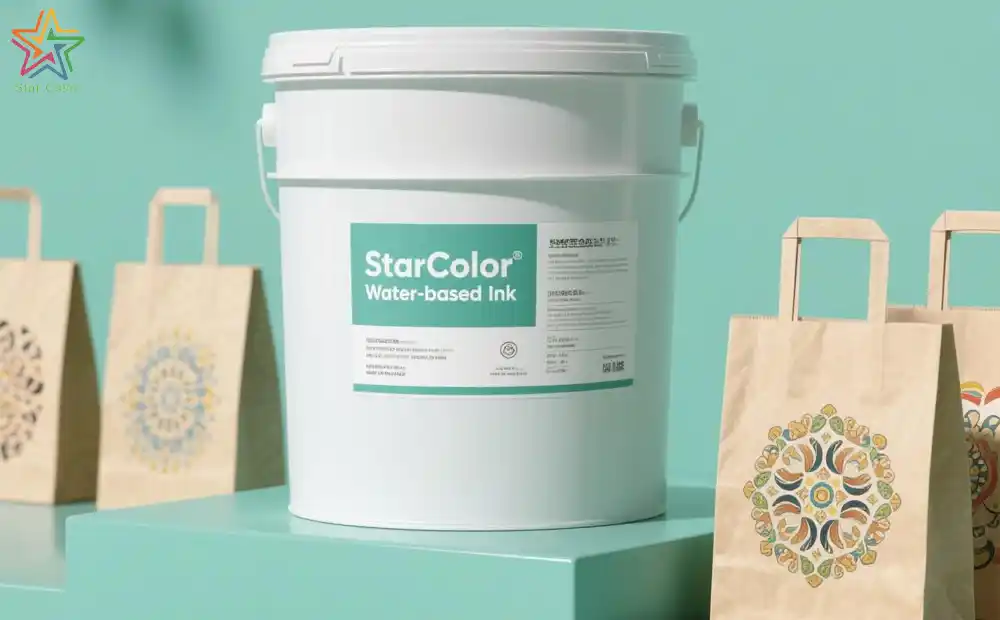
III. In-depth Performance Comparison between Water-based and Solvent-based Inks
Performance Indicators | Solvent-based Flexographic Inks | Water-based Flexographic Inks |
Drying Speed | Fast, suitable for high-speed printing | Medium speed, requiring hot air assistance |
Adhesion | Strong, suitable for various films | Dependent on corona/priming optimization |
Heat Resistance/Wear Resistance | Excellent | Good (can be improved by adjusting the formula) |
Odor | Obvious | Low odor, environmentally friendly |
Environmental Friendliness | High VOC emissions | Low VOC, no need for solvent recovery |
Cost | Stable | Slightly higher overall (but the gap is narrowing) |
It is obvious that water-based inks have approached or even come close to solvent-based inks in most indicators, and have obvious advantages in terms of environmental protection and terminal compliance.
IV. Expansion of Application Scenarios for Water-based Inks
At present, water-based inks have been successfully applied in many flexible packaging fields. In the field of fast-moving consumer goods packaging, such as biscuit and bread bags, the low odor and environmental protection characteristics of water-based inks have been fully reflected, which not only meet the safety requirements of food packaging but also conform to consumers' expectations for environmentally friendly packaging.In the field of dry goods packaging, such as rice bags and snack food packaging, water-based inks can provide good printing effects and packaging performance, ensuring the storage and transportation of products.
Labels and paper-based composite packaging are also important application fields for water-based inks. Their good adhesion and printing suitability can meet various printing requirements of labels, and at the same time, they conform to the environmental protection standards of composite packaging.
Medium and low-speed flexographic printing machines (such as CI units) also have good compatibility with water-based inks, enabling stable and efficient printing production.
However, water-based inks still need further optimization in some fields. In the field of high-speed printing (>400m/min), due to the fact that the drying speed of water-based inks still needs to be improved, it is currently difficult to fully meet the needs of high-speed production.
For substrates with extremely low surface energy, such as untreated LDPE, the adhesion of water-based inks is still problematic, and further technological improvements are needed to enhance their printing effect on such substrates.
In fields requiring extremely high heat resistance, such as microwave food packaging, the heat resistance of water-based inks needs to be further improved to ensure that the packaging will not deform, fall off, or have other problems during microwave heating.
In response to these problems, enterprises such as StarColor are actively developing the next generation of water-based flexographic inks suitable for high-speed flexography and complex composite structures, committed to expanding the application range of water-based inks while taking into account performance and environmental protection.
V. Conclusions and Future Prospects
At present, water-based flexographic inks have been widely used in flexible packaging, but there is still a long way to go to completely replace solvent-based inks. There are still challenges in terms of drying speed and adaptability to extreme substrates.Against the backdrop of global governments and brand owners promoting "green packaging", consumers' demand for environmentally friendly packaging is increasing. Water-based inks, with their environmental protection advantages, will become one of the core options for sustainable printing solutions. With the continuous progress of technology and the continuous development of the industry, it is possible that water-based flexographic inks will completely replace solvent-based inks one day in the future.