Reasons for insufficient adhesion of water-based ink when printing on woven bags
Date: Aug 25 2023 From: Star Color Views:
Insufficient adhesion of water-based ink when printing on woven bags can be caused by various factors. Here are some potential reasons for the issue:
1.Surface Preparation: The woven bags might not have been adequately prepared before printing. Dust, dirt, and residual chemicals can prevent the ink from adhering properly to the surface. Proper cleaning and pre-treatment are crucial to ensure good adhesion.
2.Material Composition: The material used for the woven bags might not be compatible with water-based inks. Some woven bags are made of low surface energy materials like polypropylene, which can be challenging for water-based inks to adhere to. In such cases, special primers or additives may be needed to improve ink adhesion.
3.Ink Formulation: The ink formulation itself could be problematic. If the ink lacks the right adhesion-promoting agents or binders, it may not adhere well to the woven bag's surface.
4.Ink Curing: Inadequate curing or drying of the ink can also lead to poor adhesion. Insufficient heat or drying time can cause the ink to remain tacky, leading to adhesion issues.
5.Incompatibility with Coatings: Some woven bags come with a protective coating to enhance durability and water resistance. If the ink is not compatible with this coating, it may fail to adhere properly.
6.Printing Process: The printing process itself could be a contributing factor. Factors like printing speed, pressure, or temperature may affect ink adhesion. An improper printing process can lead to uneven ink deposition and poor adhesion.
7.Environmental Conditions: Humidity and temperature can influence ink drying and adhesion. High humidity or low temperatures may slow down ink drying, leading to insufficient adhesion.
8.Substrate Treatment: Woven bags may require specific treatments or corona discharge to improve their surface energy, making them more receptive to water-based inks.
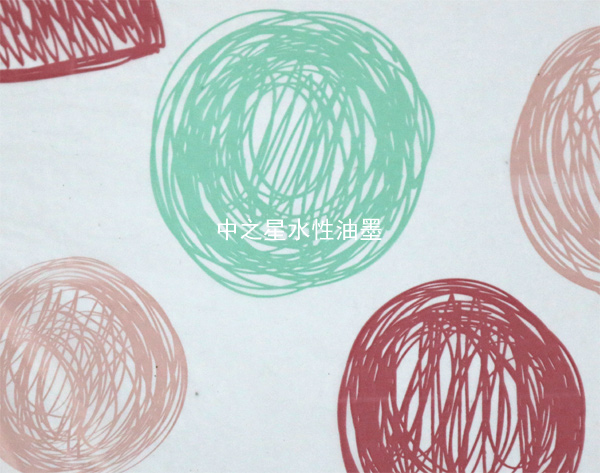
To address the issue of insufficient adhesion, you may want to consider the following steps:
1.Ensure proper surface preparation by thoroughly cleaning and treating the woven bags before printing.
2.Choose an ink formulation that is compatible with the material of the woven bags and has good adhesion properties.
3.Optimize the printing process parameters, including ink curing conditions and printing speed.
4.Test different primers or additives to enhance ink adhesion on challenging substrates.
5.Consider using heat or UV curing methods to improve ink drying and adhesion.
6.Check the compatibility of the ink with any protective coatings on the woven bags.
7.Monitor environmental conditions during printing to ensure they are conducive to proper ink drying and adhesion.
By addressing these factors, you should be able to improve the adhesion of water-based ink when printing on woven bags.