Application of Flexographic Printing on Diapers
Date: Sep 30 2024 From: Star Color Views:
In the rapidly developing personal hygiene product market, diapers are an indispensable product for newborn and elderly care, and their market demand continues to grow. With the increasing awareness of quality, safety, and environmental protection among consumers, diaper manufacturers are constantly exploring innovative technologies to provide products that are more comfortable, environmentally friendly, and have personalized designs. In this context, flexographic printing technology plays a crucial role in diaper manufacturing due to its unique advantages.
Introduction to Flexographic Printing Technology
Flexographic printing is a rotary printing method that uses flexible photosensitive resin or rubber plates for printing. Compared with traditional printing methods, flexographic printing has significant environmental benefits, as it uses water-based or UV curable inks to reduce the emission of harmful substances. In addition, flexographic printing has a short plate making cycle and strong flexibility, which can meet the rapidly changing market demand. In the field of disposable hygiene products, especially in the production of diapers, flexographic printing has become an ideal printing solution due to its high efficiency, safety, and environmental friendliness.
Application of Flexographic Printing on Diapers
Functional requirements: As a product that comes into direct contact with the skin, diapers require not only aesthetically pleasing printed patterns and text, but also good waterproof, breathable, and liquid absorbent properties. Flexographic printing technology ensures that patterns and text achieve good visual effects without affecting product functionality by precisely controlling the penetration and distribution of ink.
Appearance design: With the increasing demand for personalized product appearance from consumers, flexographic printing technology provides rich design possibilities for diapers. From brightly colored cartoon patterns to heartwarming parent-child quotes, flexographic printing can perfectly present them, helping brands enhance their market competitiveness and brand awareness.
The combination of composite technology and flexographic printing: In the production process of diapers, it is often necessary to combine fabrics of different materials together through composite technology. Flexographic printing can pre treat materials before lamination, such as creating a base color or printing moisture wicking patterns, to ensure that the resulting product is both aesthetically pleasing and practical.
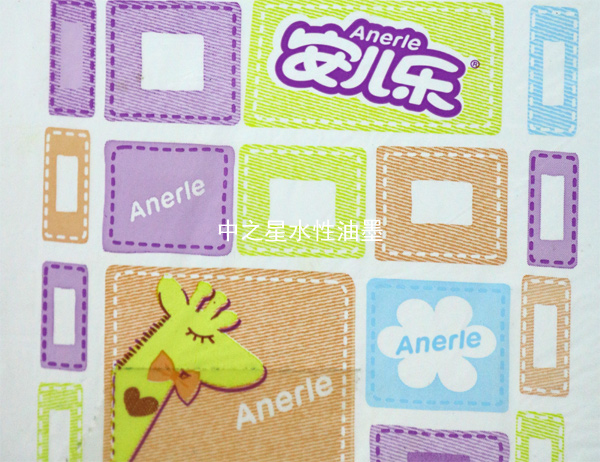
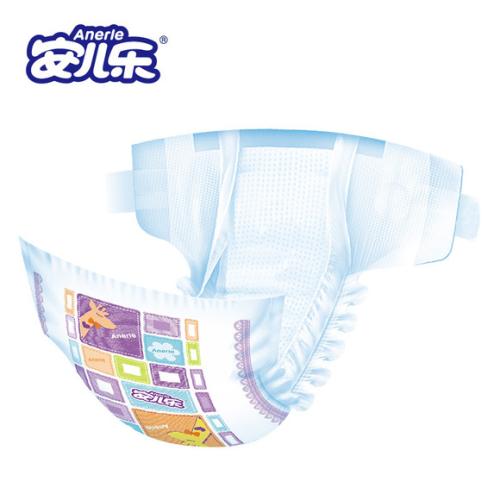
With the deepening of environmental awareness and continuous technological progress, flexographic printing technology will usher in a broader development space. In the future, the research and application of environmentally friendly inks will be more extensive, and flexographic printing equipment will also develop towards a more intelligent and efficient direction.
The application of flexographic printing technology in diaper manufacturing not only meets the dual requirements of product functionality and appearance design, but also reflects the emphasis on environmental protection and safety. With the continuous maturity of technology and the continuous development of the market, flexographic printing will play a more important role in the manufacturing of diapers, bringing consumers more high-quality and personalized product choices.
The
flexographic water-based ink produced by Zhongzhixing Color is not only safe and environmentally friendly, but also has excellent performance and wide adaptability. This ink is easy to clean and dry, with pure color, reducing the difficulty of cleaning during the production process and improving production efficiency. Its drying speed is fast, effectively shortening the production cycle. At the same time, the ink can adapt to printing materials such as non-woven fabrics and BOPP materials used for diapers, suitable for high-speed printing machines, with high printing accuracy, and can meet the aesthetic and precision requirements of diaper packaging.