Tips for Optimizing Print Quality with UV Flexo Inks
Date: Jan 10 2025 From: Star Color Views:
UV flexo printing has become a dominant choice for various packaging and label applications due to its high-quality prints, fast curing times, and eco-friendly benefits. UV flexo inks are cured by ultraviolet light, allowing for vibrant, durable prints on a wide variety of substrates, including non-porous materials like plastics and films. However, achieving optimal print quality with UV flexo inks requires careful attention to several factors, ranging from ink formulation to press setup.
1. Choose the Right UV Flexo Ink for the Substrate
Different substrates require different ink formulations. The key to achieving the best print quality with UV flexo inks starts with selecting the right ink for the material being printed on.
Tip:
- Assess the substrate type: Materials like paper, film, foil, and plastic each have unique properties that affect ink adhesion, drying speed, and appearance. UV flexo inks designed for non-porous surfaces like plastic films may have different chemical compositions compared to those formulated for paper.
- Consult with ink suppliers: Work closely with ink suppliers to choose UV flexo inks that are optimized for the specific substrate you are printing on. This will ensure proper adhesion, high-quality color reproduction, and resistance to abrasion and fading.
2. Maintain the Proper Ink Viscosity
Ink viscosity plays a critical role in print quality. If the ink is too thick, it may not transfer effectively to the substrate, causing poor coverage and low print density. On the other hand, ink that is too thin may lead to excessive dot gain, reduced sharpness, and poor detail reproduction.
Tip:
- Monitor ink viscosity regularly: Use a viscometer to check and maintain the ink viscosity within the recommended range. This will help ensure that the ink flows smoothly during the printing process without compromising print clarity.
- Adjust ink as needed: Ink viscosity can change due to temperature fluctuations, press speed, or curing conditions. Adjust the ink using the correct viscosity modifiers or thinners recommended by your ink supplier.
- Keep ink well-mixed: Inconsistent ink consistency can cause uneven color and tone. Regularly agitate the ink to maintain its uniformity.
3. Proper Plate and Anilox Roller Setup
The flexographic printing process relies on the precise transfer of ink from the anilox roller to the printing plate, which then transfers the ink to the substrate. The setup of the flexo plate and anilox roller is critical for achieving sharp, consistent prints.
Tip:
- Use the right anilox roller: The anilox roller controls the ink volume transferred to the plate, so selecting one with the appropriate cell count and volume is essential. A higher cell count may be necessary for fine detail and high-quality prints, while a lower cell count is better suited for larger, solid color areas.
- Ensure proper engraving depth: The engraving depth of the flexo plate should match the ink type and the specific application. Plates with shallow engravings may cause ink starvation, while deep engravings may lead to excessive ink transfer.
- Regularly clean and maintain rollers and plates: Dirty or worn-out plates and anilox rollers can lead to inconsistent ink transfer, resulting in poor quality prints. Ensure that all rollers and plates are cleaned regularly to maintain print quality and minimize downtime.
4. Control UV Curing and Drying Conditions
The curing process is vital to achieving high-quality prints with UV flexo inks. Proper curing ensures that the ink adheres well to the substrate, is resistant to scratching, and maintains its color intensity. Insufficient or inconsistent curing can lead to poor adhesion, dull prints, and reduced durability.
Tip:
- Calibrate UV curing lamps: Ensure that UV lamps are properly calibrated for the ink and substrate combination. Use UV radiometers to measure the intensity of the UV light and verify that it is within the optimal curing range.
- Maintain consistent exposure: Ensure that all areas of the printed material are exposed to consistent UV light for uniform curing. Uneven exposure can lead to curing defects such as sticky spots, reduced gloss, and poor ink adhesion.
- Optimize curing speed: The speed of the print press and the distance from the UV lamp to the substrate must be carefully balanced. If the press speed is too high or the substrate is too far from the curing lamp, the ink may not cure completely. Conversely, excessive exposure can cause over-curing, which might affect the gloss and surface properties.
5. Regularly Check Ink Film Thickness
The thickness of the ink film directly impacts print quality. If the ink layer is too thin, the printed colors may appear faded or washed out. If the ink film is too thick, it may result in excessive dot gain, loss of fine detail, and a heavy ink build-up on the substrate.
Tip:
- Use a densitometer or spectrophotometer: Regularly measure the ink film thickness to ensure that it is within the optimal range for your specific application.
- Adjust anilox roller settings: If ink coverage is uneven, you may need to adjust the settings of your anilox roller or the ink viscosity to maintain consistent ink transfer.
- Optimize print pressure: Make sure that print pressure is appropriately adjusted for the ink and substrate, as excessive pressure can cause ink over-application, while insufficient pressure may lead to poor ink transfer.
6. Optimize Press Speed and Tension
Press speed and substrate tension play a significant role in the overall print quality. Incorrect speed or tension settings can cause issues such as misregistration, poor ink transfer, and uneven color distribution.
Tip:
- Adjust press speed according to substrate and ink type: Ensure that the press speed is optimized for the ink formulation and substrate type. Faster speeds can be achieved with UV inks, but the optimal speed may vary depending on the substrate’s absorbency and the curing system’s efficiency.
- Maintain consistent web tension: Proper tension helps maintain accurate print alignment, reducing issues such as image distortion or misregistration. Use tension control devices to monitor and maintain consistent web tension throughout the print job.
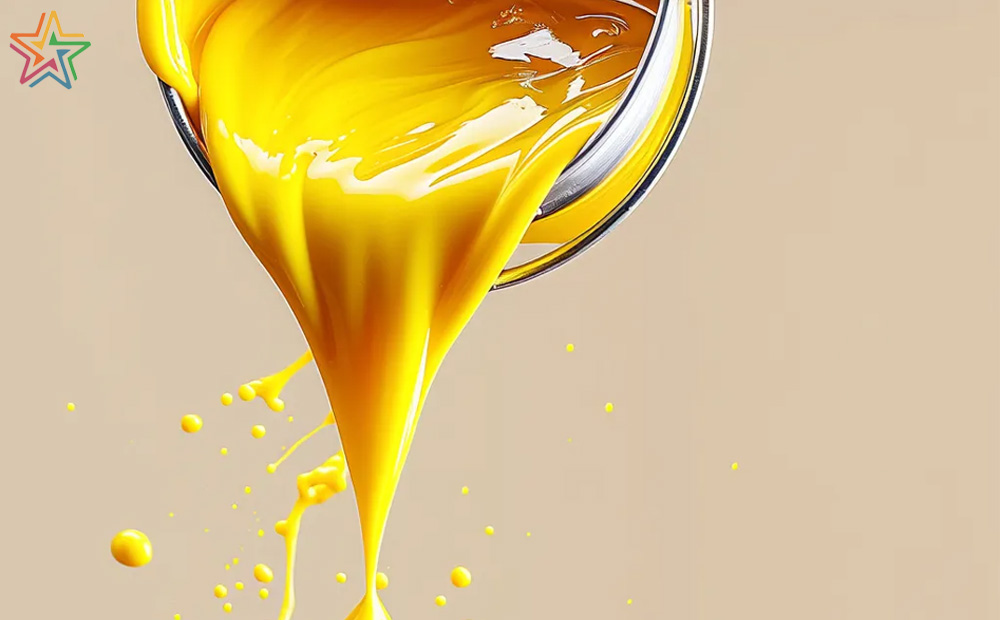
Optimizing print quality with UV flexo inks requires a holistic approach that involves selecting the right ink and substrate, managing press parameters, ensuring accurate color reproduction, and performing regular maintenance. By following the tips outlined in this article—such as adjusting ink viscosity, optimizing UV curing conditions, and maintaining proper equipment settings—you can achieve high-quality, consistent prints that meet customer expectations and enhance your brand's appearance.