The Advantages of Starcolor Customized Flexographic Ink Formula in Food Packaging
Date: Jul 24 2025 From: Star Color Views:
1. Customized Safety and Compliance
The safety bottom line for food packaging is that inks must not migrate to food, and compliance standards vary across regions – the US FDA has migration limits for food contact materials, the EU EFSA has its own substance lists, and China's GB 4806 series standards focus on different aspects. Starcolor's core advantage lies in "customized adaptation":- For customers exporting to Europe, it can meet the REACH SVHC regulations;
- For enterprises targeting the North American market, formulations are optimized to pass FDA migration tests (such as the 10% ethanol immersion test);
- For products sold in China, it strictly adheres to the additive usage specifications in GB 9685.
This customized adjustment based on target markets eliminates customers' worries about "exceeding standard risks" with universal formulations, truly achieving "compliance in one region, adaptation globally".
2. Customized Matching of Substrates and Processes
The visual appeal of food packaging relies on in-depth collaboration between inks, substrates, and printing processes, and such collaboration must be achieved through customization. For example:- For smooth BOPP films, Starcolor customizes formulations containing special adhesion promoters to solve the ink detachment problem caused by low surface energy;
- For porous food-grade cardboard, it adjusts the ink penetration rate to avoid color graying due to excessive absorption.
Even for the same substrate, customization can accurately respond to different printing processes: when a matte effect is required, the proportion of matting resin is increased; for a glossy effect, leveling agents are optimized to ensure color saturation and gloss fully meet brand design requirements. This dual-dimensional customization of "substrate + process" ensures zero deviation of printed patterns from design drafts to finished products.
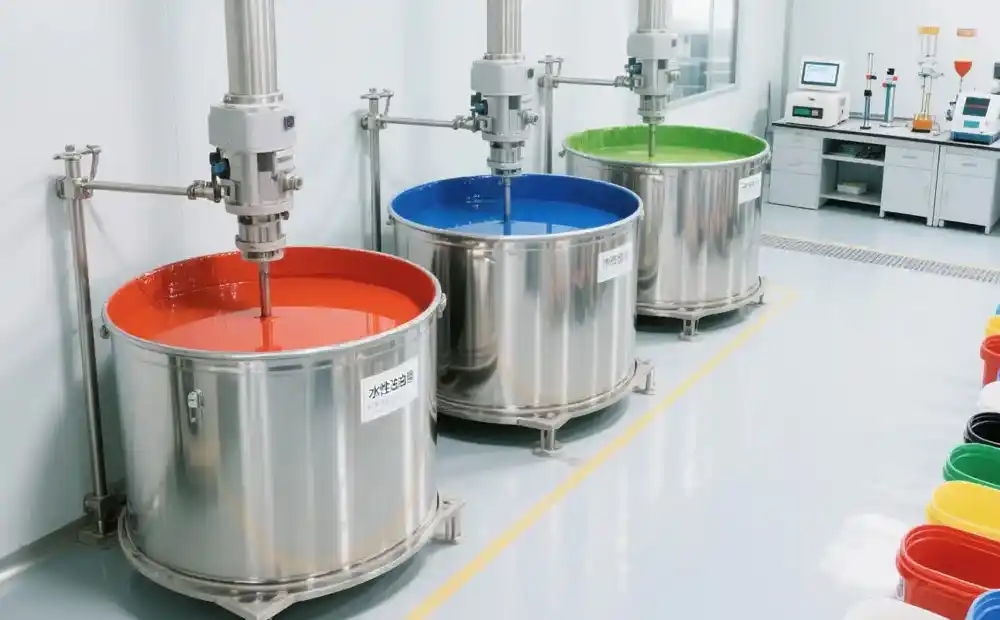
3. Customized Weather Resistance and Resistance Properties
Problems with food packaging sometimes stem from the food itself – the corrosion of acidic beverages, high-temperature grease from fried foods, and low-temperature humidity from frozen foods, each scenario having distinct resistance requirements for inks. Starcolor's customization demonstrates key value here:- For pickled food packaging, a acid-resistant resin system is customized to ensure the ink does not decompose in environments with a pH value below 3.0;
- For baked food packaging, heat resistance is enhanced to over 120°C to avoid ink softening caused by high temperatures;
- For cold-chain food packaging, anti-condensation ingredients are added to prevent ink whitening during refrigeration.
This approach of "customizing protection according to food types" ensures the packaging remains fully functional throughout the entire cycle from production to consumption.
4. Customization for Machine Models and Equipment
Differences in food packaging production equipment directly determine whether inks can operate efficiently, and Starcolor's customization targets core equipment parameters:- For printing machines:
- Satellite printing machines, with stable tension and high speed (up to 400 meters per minute), require customized high-fluidity inks to reduce ink transfer resistance;
- Unit-type printing machines, due to frequent substrate switching, focus on adjusting ink adaptability to ensure no re 调试 is needed when switching between films and cardboard.
- For anilox roller line counts:
- For anilox rollers with 300+ lines (requiring fine pattern printing), ink particle size is customized to below 5μm to avoid mesh clogging;
- For 100-200 line anilox rollers (used for large-area printing), solid content is increased to over 45% to ensure a thick and uniform ink layer.
This "equipment parameter customization" directly improves production efficiency – customers no longer need to frequently adjust equipment for universal inks, reducing ink consumption by 10%-15% and downtime by over 30%.
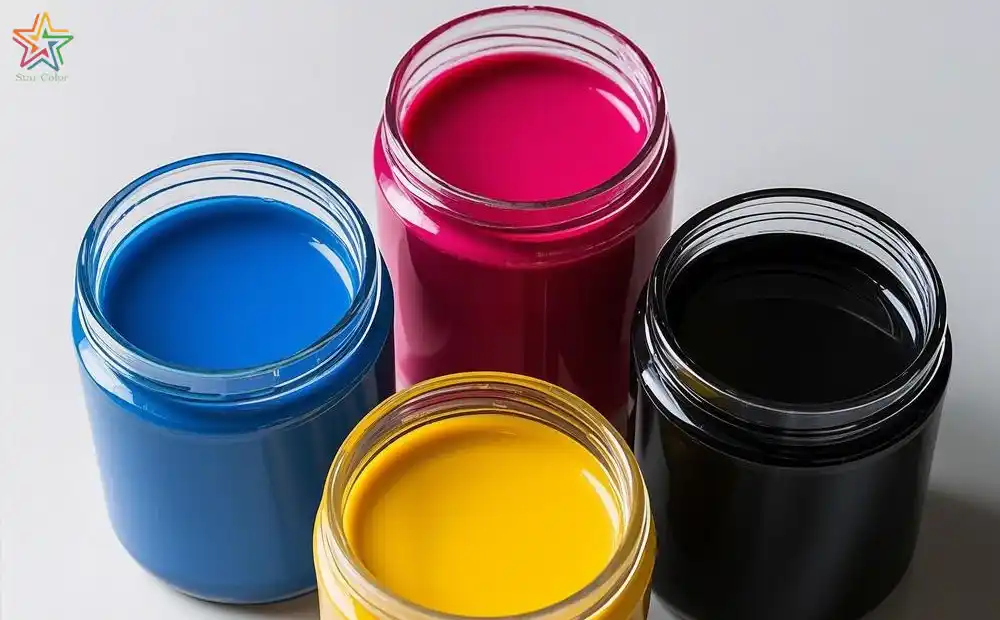